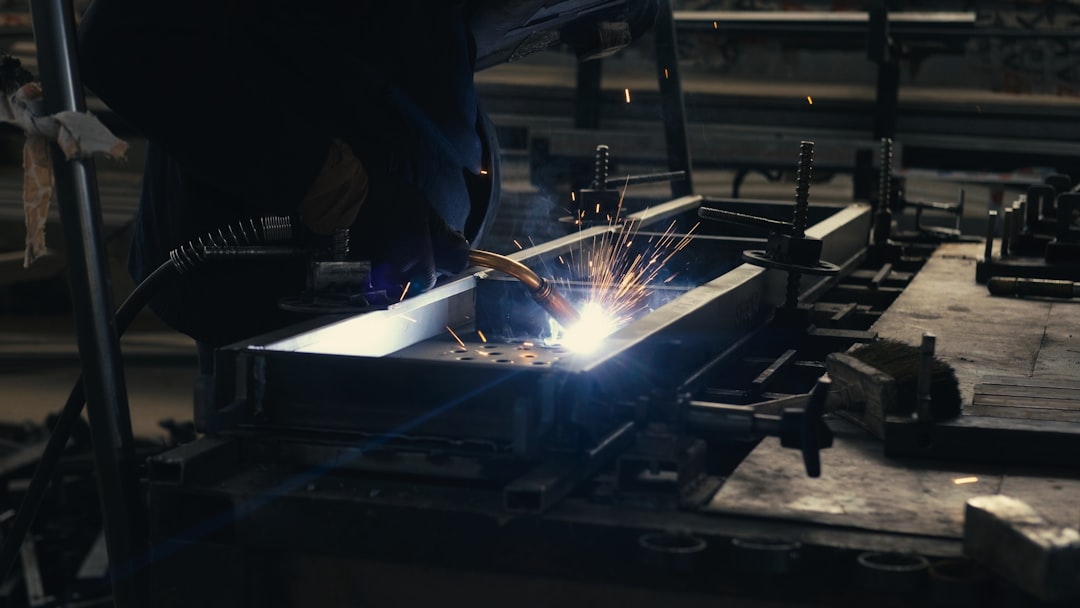
Protect yourself with expert welding PPE recommendations. Learn essential gear, safety tips, and compliance for every welding job.
Welding PPE recommendations are critical for every welder who wants to keep their eyesight, skin, and lungs intact. Burns are the most common injury to welders, but with the right gear, 90% of workplace eye injuries and 60% of hand injuries are completely preventable.
Essential Welding PPE (Quick Reference):- Head/Eyes: Auto-darkening helmet (shade 8-14) + ANSI Z87.1 safety glasses- Hands: Process-specific gloves (TIG: thin leather, MIG/Stick: heavy leather)- Body: Flame-resistant jacket/apron, avoid all synthetic fabrics- Feet: Steel-toe leather boots + spats for heavy work- Lungs: P100 respirator when welding stainless or in confined spaces- Ears: Earplugs/earmuffs (welding noise ranges 85-120 dB)
Welding exposes you to temperatures up to 10,000°F, intense UV radiation that can cause "arc eye," toxic fumes, and molten metal splatter. The right PPE isn't just about avoiding injuries—it's about protecting your ability to work and provide for your family.
Professional welders face unique risks that hobbyists don't. You're dealing with higher amperages, longer exposure times, and often working in confined spaces or with exotic alloys that produce dangerous fumes like hexavalent chromium.
I'm William "Stick" Mank, a second-generation welder with over 20 years in the oil and gas industry, and I've seen too many good welders get hurt because they cut corners on safety gear. My welding PPE recommendations come from real-world experience in extreme conditions where cheap gear fails and proper protection saves careers.
After two decades under the hood I’ve learned one rule: welding PPE recommendations are life support, not suggestions. Every welder I’ve seen skip proper gear—usually to save time or a few dollars—ended up injured or out of work.
Welding can hurt you in seconds. An arc tops 10,000 °F and plasma cutting can reach 50,000 °F—hotter than the sun’s surface. Expose skin or eyes for even a blink and you’re headed to the burn unit.
Trying to “save” $200 on a respirator can lead to $25,000 in hospital bills. Flash-burn ER visits cost $2-5 k, while surgery for severe hand injuries can top $40 k. Chronic lung problems from fume exposure? Plan on $50 k or more over time.
Lost-time injuries average 8-12 workdays—about $1,600-$2,800 in missed wages for a $30/hr welder. Add reduced dexterity, damaged vision, or long-term breathing issues, and the real price of cheap or missing PPE is a shorter, less profitable career.
When it comes to welding PPE recommendations, we don't mess around at Tentacle Tools. After decades in the oil and gas industry, I've learned that proper protection isn't just about meeting ANSI Z49.1 and CSA Z94.3 standards—it's about getting home safe every day with all your parts intact.
Think of PPE as your armor against the battlefield of welding. We start at the top and work our way down, because every piece of equipment has to work together as a system. Skip one component, and you've got a weak link that could cost you dearly.
Here's something that might surprise you: even with a welding helmet, you absolutely need safety glasses underneath. I can't tell you how many times I've seen welders get debris in their eyes during grinding, wire brushing, or just moving around the job site with their helmet up.
The science backs this up completely. Scientific research on preventing eye trauma shows that 90% of workplace eye injuries are completely preventable with proper eyewear. That's a statistic worth paying attention to.
ANSI Z87.1 compliance isn't just a suggestion—it's your guarantee that the glasses can actually protect you. Look for impact resistance testing, mandatory side shields, and proper UV and IR radiation filtering. The glasses should have clear markings showing they meet compliance standards.
When selecting safety glasses for welding work, go for a wraparound design with side shields that fits comfortably under your helmet. Anti-fog coating is worth every penny in humid conditions, and scratch-resistant lenses will last longer in the harsh welding environment.
Your welding helmet is your most critical piece of protection, and there's really no contest between auto-darkening and fixed-shade helmets anymore. Auto-darkening helmets offer superior safety and convenience, allowing you to see clearly during setup and automatically adjusting in 1/10,000th of a second when the arc strikes.
The optical quality rating system uses four numbers (1/1/1/1 is the best) representing optical class, light diffusion, luminous transmittance variation, and angular dependence. Don't settle for anything less than top-tier optics when your eyesight is on the line.
Shade selection depends on your welding process and amperage. TIG welding typically needs shade 8-13, MIG welding requires shade 10-13 for most applications, and stick welding calls for shade 10-14 for heavy-duty work. Plasma cutting falls in the shade 8-12 range based on current.
Look for features like adjustable shade ranges, memory settings for different processes, and solar power with battery backup. The viewing area should be around 50 x 100mm—big enough for good visibility without making the helmet too heavy.
Here's my golden rule for welding gloves: don't try to save money on gloves—your hands are probably your most valuable tool. The right gloves can make the difference between precise, quality work and struggling through every weld.
TIG welding demands thin, flexible gloves made from goat, deer, or sheepskin for maximum dexterity. You need that precise torch control, so look for a tight fit with ATPV ratings around 8-12 cal/cm² and short cuffs that won't interfere with wrist movement.
MIG welding calls for medium-weight cowhide or pigskin with heat-resistant liners for comfort. ATPV ratings should be 20-30 cal/cm² with gauntlet cuffs to protect your forearms from spatter.
Stick welding requires the heavy artillery—thick elk hide or heavy cowhide with Kevlar® stitching for durability. Look for ATPV ratings of 30+ cal/cm² and extended cuffs that overlap your jacket sleeves.
Key features across all glove types include reinforced palms and fingertips, seamless fingertip construction for better feel, moisture-wicking liners, and easy on/off design for efficiency between welds.
Let me be crystal clear about this: synthetic fabrics have no place in a welding environment. Polyester, acetate, and acrylic can melt and stick to your skin when ignited, causing horrific burns that I wouldn't wish on anyone.
Stick with natural fibers or properly treated FR materials that meet ISO 11611 standards. 100% cotton with FR treatment, wool (which is naturally flame-resistant), leather for heavy-duty work, and Kevlar® blends for extreme heat are your best bets.
Essential features include chest pocket flaps to keep sparks out, snap or Velcro closures instead of buttons that can catch, no cuffs on pants or sleeves, and tight weave construction to resist spark penetration.
Your feet take a beating in welding environments, and basic steel-toe boots just aren't enough. You need high-top leather construction with 6-8 inch ankle coverage, steel or composite toe protection, and metatarsal guards for heavy industrial work.
Slip-resistant soles are crucial for oily surfaces, and electrical hazard protection can save your life. Consider accessories like leather spats that strap over your boots for spark protection and fire-resistant boot protectors for areas with heavy slag.
Hearing protection is often overlooked until it's too late. Welding environments generate 85-120 decibels of noise, and OSHA requires hearing conservation programs when noise exceeds 85 dBA averaged over eight hours.
Your options include disposable foam earplugs for 25-33 dB reduction, reusable silicone plugs for comfort during long shifts, fire-resistant earmuffs to prevent spark entry, and electronic earplugs that allow communication while still protecting your hearing.
This is where many welders make a critical mistake—ignoring respiratory protection until health problems develop. Welding fumes contain numerous toxic substances, and long-term exposure can cause serious respiratory and neurological damage that will end your career.
Respiratory protection becomes critical when welding stainless steel (hexavalent chromium exposure), working in confined spaces with poor ventilation, welding painted or galvanized materials, during extended welding sessions, or any time you can taste metal in your mouth.
Half-face respirators with P100 filters work for general welding applications and capture 99.97% of particles. Powered Air-Purifying Respirators (PAPR) are essential for confined spaces and stainless steel welding, providing positive pressure to keep contaminants out.
Only complete PAPR systems receive NIOSH certification—you can't mix and match components from different manufacturers. Make sure your system includes proper filters, breathing tubes, and power supplies from the same certified manufacturer.
After two decades of welding everything from delicate aluminum tubing to thick-wall pressure vessels, I've learned that welding PPE recommendations must match your specific process. What protects you during precision TIG work might leave you vulnerable during heavy stick welding, and vice versa.
The key is understanding how each welding process creates different hazards. TIG welding produces intense UV radiation but relatively little spatter, while stick welding throws hot slag everywhere but operates at lower UV levels. Your PPE needs to match these unique challenges.
TIG welding demands maximum dexterity and vision. You're working with precise torch angles and tight fitups, so bulky gloves and heavy clothing get in the way. However, the argon shielding gas can displace oxygen in confined spaces, making respiratory protection critical. The intense arc also produces more UV radiation per amp than other processes.
MIG welding sits in the middle ground for PPE requirements. You'll deal with moderate spatter and heat, requiring gear that balances protection with mobility. The continuous wire feed creates steady fume production, so ventilation becomes more important than with intermittent processes like stick welding.
Stick welding hits you with everything at once—heavy spatter, hot slag, and the highest heat exposure of common welding processes. Your PPE needs to handle the punishment while keeping you comfortable enough to maintain good technique through long welding sessions.
Getting your helmet shade right is crucial for both safety and weld quality. Too dark and you can't see the puddle properly. Too light and you risk permanent eye damage. I always tell new welders to start with a shade that's too dark, then work down until they can see clearly while still feeling protected.
For TIG welding, amperage drives your shade selection more than material thickness. Start with shade 10 for most work under 80 amps, then move up to shade 12-13 for high-amperage applications. The clean arc gives you good puddle visibility even through darker filters.
MIG welding typically requires shade 11-12 for most applications. The spray transfer and spatter create more light than TIG, so you need the extra protection. Pulse MIG can be tricky—the varying amperage means you might need shade 13-14 to handle the peak currents.
Stick welding shades run from 10-14 depending on electrode size and amperage. A 1/8" 7018 rod at 120 amps needs about shade 11, while a 5/32" rod at 180 amps pushes you toward shade 13. The slag and spatter make puddle visibility challenging, so don't go darker than necessary.
These are starting points. Your eyes, the specific equipment, and working conditions all affect what shade works best for you. Trust your comfort level—if your eyes feel strained or you're getting headaches, try a darker shade.
Some welding environments throw the standard welding PPE recommendations out the window. Working in refineries, offshore platforms, and pipeline right-of-ways has taught me that extreme conditions require extreme protection measures.
Confined space welding changes everything. The normal PPE that keeps you safe in open air becomes inadequate when you're inside a pressure vessel or tank. Supplied-air respirators become mandatory because even small amounts of welding fumes concentrate quickly. You need communication systems to stay in contact with your fire watch, and emergency evacuation procedures become life-or-death critical.
Outdoor pipeline work presents its own challenges. Weather protection becomes part of your PPE system—wind screens protect your arc and prevent fume dispersion, while weather-resistant gear keeps you dry and functional. High-visibility clothing is often required near traffic or heavy equipment operations.
High-amperage welding applications like submerged arc or heavy fabrication require upgraded heat protection. Standard leather jackets aren't enough when you're running 400+ amps. Aluminized clothing reflects radiant heat, while improved ventilation systems become necessary to handle the increased fume production.
Welding chromium alloys like stainless steel requires specialized respiratory protection beyond basic P100 filters. The hexavalent chromium produced is a known carcinogen, making PAPR systems with HEPA filtration essential for regular exposure. Many companies now require medical surveillance programs for welders working with these materials.
The bottom line is simple: when working conditions get extreme, your PPE needs to match. Don't try to make standard gear work in non-standard situations. Your health and your ability to provide for your family depend on using the right protection for the job at hand.
Taking care of your PPE isn't just about making it last longer—it's about making sure it'll protect you when you need it most. I've seen too many welders with gear that looked fine on the outside but failed when it mattered. The good news is that proper maintenance doesn't take much time, and it can save your life.
Your welding PPE recommendations mean nothing if you don't maintain the gear properly. Think of it like your welding machine—you wouldn't skip maintenance on a $5,000 welder, so why skip it on the gear protecting your eyes and lungs?
Daily checks should become as automatic as putting on your boots. Before you strike the first arc, take two minutes to inspect your helmet lenses for cracks or scratches that could compromise your vision. Check your gloves for holes or worn spots—leather that's cracked or stiff won't protect against heat or electricity.
Your clothing needs attention too. Look for frayed edges, burn holes, or areas where the flame-resistant treatment might be wearing off. If you're using respiratory protection, test the seal and check your filters. Those P100 filters don't last forever, and a clogged filter is almost as bad as no filter at all.
Weekly deep cleaning keeps everything in working order. Clean the inside of your helmet where sweat and dirt build up. This isn't just about comfort—moisture and grime can interfere with the electronics in auto-darkening helmets. Condition your leather gear to prevent cracking, and replace any worn gaskets or retainers in your helmet.
Storage matters more than most people realize. Keep your gear in a cool, dry place away from direct sunlight. UV rays that are tough on your skin are just as hard on your PPE. Make sure contaminated gear stays separate from clean equipment, and ensure good ventilation to prevent moisture buildup that can cause mold or equipment failure.
OSHA standards 1910.252 through 1910.254 cover welding safety requirements, and they're not just suggestions. OSHA recommends safe welding PPE and requires employers to provide appropriate protective equipment at no cost to employees. This means if you're working for someone else, they need to supply and maintain your safety gear.
Training logs and documentation protect everyone involved. Keep records of when people were trained on PPE use, what equipment they're qualified to use, and when their training expires. It might seem like paperwork for the sake of paperwork, but these records can be the difference between a minor OSHA citation and a major legal problem if someone gets hurt.
If you're using respirators regularly, you need to take fit testing seriously. This isn't just a box to check—it's about making sure the equipment actually seals properly on your face. A respirator that doesn't fit is worse than no respirator at all because it gives you false confidence while letting contaminated air leak in around the edges.
Annual fit testing is mandatory for anyone using tight-fitting respirators. This includes half-face masks, full-face respirators, and any other equipment that relies on a seal against your skin. The test needs to be repeated if you have significant weight changes, dental work, or facial injuries that might affect the fit.
Documentation requirements include initial and annual fit testing records, training verification, equipment inspection logs, and any incident reports. Keep track of when equipment was purchased, when it needs replacement, and any maintenance performed. Medical surveillance records are required for workers with significant exposure to hexavalent chromium or other carcinogens.
Modern tracking systems can make this easier. QR code labels on equipment link to digital inspection forms and maintenance schedules. Automated reminders help ensure nothing gets forgotten, and digital records are easier to organize and access during inspections.
The key is building these habits into your routine until they become second nature. Good welders don't just lay perfect beads—they take care of themselves and their equipment so they can keep welding for decades to come.
Over the years, we've answered thousands of questions from welders who want to make smart decisions about their safety gear. These are the three questions that come up most often, and they're all great questions that show you're thinking seriously about protection.
Your gloves are telling you when they need replacement—you just need to listen. When you notice holes, cracking, or stiffness that affects your grip, it's time for new gloves. If you're losing dexterity or feeling more heat than usual, don't push it another day.
For professional welders working daily shifts, quality gloves typically last 2-4 months depending on your welding process. TIG welders often need replacement more frequently because those thin gloves take a beating, while heavy-duty stick welding gloves might last longer with proper care.
Helmet lenses need attention when they're scratched, hazy, pitted, or cracked. Here's a pro tip that'll save you money: use cover plates to protect your expensive filter lens. We always keep spare cover plates handy for quick changes during the workday.
Auto-darkening filter cartridges are built to last 5-7 years with proper care, but they're not indestructible. If your helmet isn't darkening consistently or you're seeing spots in your vision, replace the cartridge immediately—your eyesight is worth more than any lens.
Absolutely yes, and here's why this matters so much. Your helmet protects you during welding, but what about the other 40% of your day? When you're grinding, cleaning slag, or setting up your next pass, that helmet is up and your eyes are exposed.
Safety glasses provide backup protection against ricocheting sparks and debris that might sneak under your helmet shell. Even the best auto-darkening helmets can fail—batteries die, sensors get dirty, and electronics break down. When that happens, safety glasses are your lifeline.
Choose ANSI Z87.1 compliant safety glasses with side shields that fit comfortably under your helmet. The small investment in quality eyewear is nothing compared to emergency room bills for eye injuries. Trust me, I've seen welders learn this lesson the hard way.
Respirators become mandatory the moment you strike an arc on stainless steel, especially in confined spaces or areas with poor ventilation. The hexavalent chromium produced during stainless steel welding is a known carcinogen that requires serious protection.
For general stainless steel welding, use respirators with P100 filters that capture 99.97% of particles. When you're working extended periods or in tight spaces, upgrade to PAPR systems that provide positive pressure and better protection.
The key is conducting proper hazard assessment before you start welding. If you can taste metal in your mouth or smell fumes, you need respiratory protection immediately. OSHA 29 CFR 1910.134 requires respiratory protection programs for good reason—your lungs can't be replaced.
Don't gamble with your health on stainless work. The welding PPE recommendations for respiratory protection exist because we've learned what happens when welders skip this critical step. Invest in proper respiratory gear and use it consistently—your future self will thank you.
At Tentacle Tools, we stand behind the welders who keep America's infrastructure strong. Our welding PPE recommendations aren't just theory—they come from decades of real experience in oil and gas fields where safety mistakes can end careers or worse.
We've seen too many good welders get hurt because they thought they could save a few bucks on protection gear. The truth is, cutting corners on PPE always costs more in the long run. A $200 helmet beats a $20,000 medical bill every single time.
The skilled trades built this great nation through hard work, grit, and determination—values we're proud to support alongside the American flag and the bald eagle that represents our strength. But even the toughest welders need proper protection to keep doing what they do best.
Quality PPE isn't about following rules for the sake of it. It's about respecting yourself and your craft enough to do it safely. The pipeline welders and industrial professionals we work with understand something important: proper protection makes you a better welder, not a weaker one.
When you can see clearly through a quality helmet, work comfortably in well-fitted gloves, and breathe easily with proper respiratory protection, your welds improve. Your productivity goes up. Your career lasts longer.
Our mission goes beyond manufacturing specialty welding tools. Through our dedicated job board, we connect skilled tradespeople with opportunities across the United States. We're here to support the community that keeps America running strong.
Don't get torched by preventable injuries. Follow our welding PPE recommendations, take care of your equipment, and never compromise on the basics. Your vision, your hands, your lungs, and your career are irreplaceable—protect them with the head-to-toe approach we've laid out.
For more information about welding safety resources and proper PPE selection, visit the American Welding Society safety guidelines and remember: the best PPE is the gear you actually wear every single day. Stay safe out there, and keep building America one solid weld at a time.
Explore insights, tips, and trends in tech and productivity!