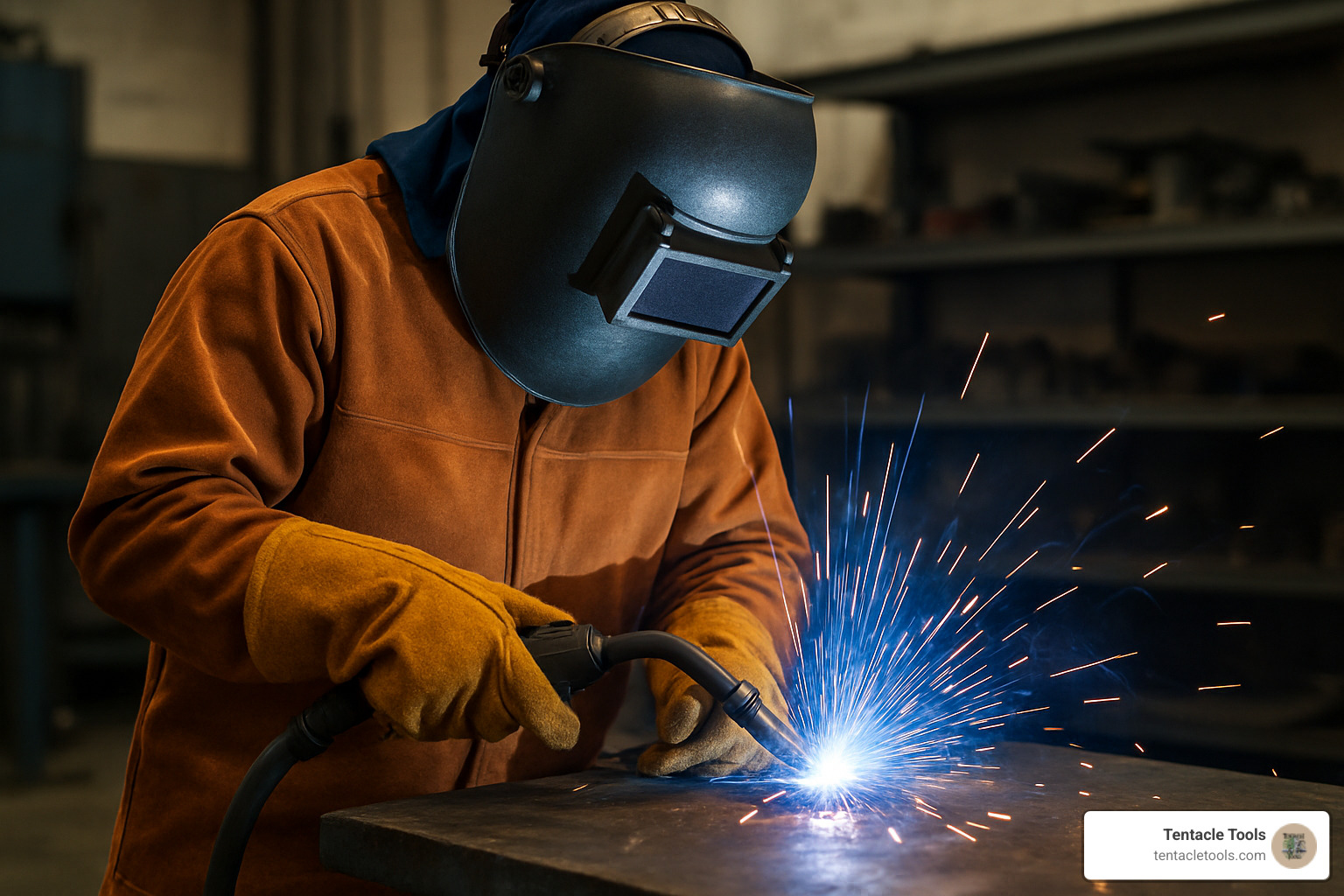
Stay safe at work—discover how to choose welding apparel for maximum protection, comfort, and compliance with safety standards.
Welding apparel is specialized clothing designed to protect welders from sparks, intense heat, molten metal, and harmful radiation during welding. It includes jackets, shirts, pants, aprons, sleeves, caps, and chaps made from flame-resistant (FR) materials such as leather or treated cotton.
Key Points:- Purpose: Shields skin and clothing from burns, electric shock, and UV/infrared (IR) radiation.- Types of Garments: Jackets, shirts, pants, aprons, sleeves, caps, chaps.- Best Materials: Leather (durable, heat-resistant), FR cotton (breathable, lightweight), wool, and specialized fabrics like CarbonX.- What to Avoid: Synthetics (polyester, nylon) can melt and stick to skin, causing severe injuries.- Why It Matters: Over half a million U.S. workers are at risk for welding-related injuries each year.
Wearing proper welding apparel is a non-negotiable—cheap or incorrect clothing won't cut it if you want long-term protection on the job.
My name is William "Stick" Mank. After 20+ years in the oil and gas fields and as the founder of Tentacle Tools, I've lived through every pitfall and breakthrough in welding apparel—designing, wearing, and repairing gear built to survive the real world.
When I first started welding in the oil fields, an old-timer told me something I'll never forget: "The arc doesn't care if you're tough—it'll burn you just the same." He was right. Welding apparel isn't about looking professional (though that's nice)—it's about going home in one piece every single day.
Every time you strike an arc, you're releasing forces that reach 10,000°F—literally hotter than the surface of the sun. That kind of heat creates a perfect storm of hazards that regular work clothes simply can't handle.
Sparks and spatter are the obvious threats. These aren't just little orange specks—they're molten metal particles flying at high speed, ready to embed themselves in any fabric that can't resist them. I've seen cotton t-shirts go up in flames from a single spark.
But the dangers go deeper. Radiant heat will cook your skin even without direct contact, while UV and infrared radiation work like an invisible sunlamp, causing burns you won't feel until it's too late. Then there's the risk of electric shock from current flowing through sweat-dampened clothing, and molten metal droplets that can penetrate regular fabrics like they're made of paper.
Here's a sobering reality check: more than 500,000 U.S. workers face welding-related injury risks every year. That translates to roughly 60 fatalities annually in our industry. These aren't just statistics—they represent real people with families, dreams, and bills to pay.
OSHA regulation 1910.252(b)(3) and ANSI Z49.1:2021 standards aren't bureaucratic paperwork—they're lifelines written in legal language. These regulations require protective clothing that minimizes ignition potential, prevents burns from trapped sparks, and reduces electric shock risks.
The bottom line? Proper welding apparel isn't an expense—it's an investment in your future. You can't put a price on walking away from every job site with all your parts intact and your family knowing you're coming home safe.
For the latest guidance on welding safety apparel, industry standards continue to evolve as we learn more about protecting the people who build America's infrastructure.
After two decades of getting burned (literally and figuratively), I've learned that knowing your welding apparel options can make or break your career. Let me walk you through what actually works in the real world.
Welding jackets are your bread and butter for upper-body protection. A good jacket covers you from neck to waist with full sleeves that won't ride up when you're reaching overhead. The magic is in the details—snap closures instead of zippers (trust me, melted zippers are a nightmare), no front pockets to catch sparks, and under-arm vents so you don't cook yourself on hot days.
Welding shirts work great as your base layer or standalone protection for lighter work. FR cotton shirts breathe well while keeping you safe from flash burns. Welding pants need to cover your legs completely without cuffs that trap sparks. Heavy-duty denim or FR-treated cotton does the job for most welding.
Welding aprons give you targeted protection when you need mobility more than full coverage. Welding sleeves protect your arms when a full jacket feels like wearing a sauna suit. Don't forget your head—welding caps protect your scalp and hair from sparks and UV rays.
The construction details matter more than you might think. Quality welding apparel uses Kevlar thread that won't burn through when hot metal hits it. Hi-vis options are becoming standard in many industrial settings.
The type of welding you do determines how much armor you need. Light-duty TIG work produces less spatter and runs cooler, so FR cotton shirts and lightweight gear work well. The key is breathability—you're doing precision work that requires steady hands, not fighting overheating.
Heavy-duty MIG and stick welding is a different animal entirely. You need leather jackets and aprons that can handle serious spatter without flinching. CarbonX materials resist the worst abuse, and you'll want to look for ATPV ratings if you're doing any arc-flash work.
Getting the fit right is where most people mess up. Coverage from neck to ankle is non-negotiable, but you also need to move freely. Your sleeves should reach your wrists when you extend your arms, and your jacket should overlap your pants by several inches.
Cuff design matters more than you'd think. Tight cuffs under your gloves prevent gaps where sparks sneak in. Women-specific cuts are finally available from quality manufacturers, providing better fit without sacrificing protection.
Most good brands now offer extended sizes from XS to 8XL, so everyone can find gear that actually fits. Proper fit isn't just about comfort—poorly fitted welding apparel leaves gaps in your protection that can cost you skin.
For more detailed guidance on selecting the right protective clothing, check out the latest guidance on welding safety apparel. And if you want to dive deeper into jacket selection specifically, What is a Welding Jacket? covers the technical details.
When it comes to welding apparel, the fabric you choose isn't just about comfort—it's literally about keeping your skin intact. After two decades of testing materials in everything from pipeline trenches to offshore rigs, I can tell you that understanding fabric science will save you from painful mistakes.
Leather has protected welders for generations, and there's good reason it's still the go-to choice for heavy-duty work. When sparks hit leather, they bounce off or burn out harmlessly. Cowhide delivers maximum durability and heat resistance—perfect for stick welding and heavy fabrication. Goatskin gives you better flexibility for precision work.
The downside? Leather gets hot and doesn't breathe much. But when molten metal is flying, that trade-off makes sense.
FR cotton has become our everyday choice for most welding tasks. Heavy-weight cotton at 9 ounces or more gives you solid spark resistance while letting air flow through. The key is finding cotton that's been properly treated to maintain its flame-resistant properties through dozens of wash cycles.
Regular denim made from 100% cotton provides natural flame resistance at a price that won't break the bank. It's not as protective as specialized FR fabrics, but it's a solid choice for general welding work. Just make sure it's pure cotton—no blends.
Wool excels when you're welding in cold conditions. It naturally resists flames and keeps you warm even when wet.
CarbonX represents the latest evolution in welding protection. This lightweight material feels less bulky than leather but handles sparks and molten metal even better. Aramid fibers like Kevlar bring inherent flame resistance that never washes out.
Inherent flame resistance means the protection is built into the fiber itself. Treated flame resistance relies on chemicals applied to the fabric. Inherent costs more but lasts longer because the protection can't wash out.
The industry uses several key standards to measure protection. ASTM D6413 sets testing standards for flame-resistant workwear. NFPA 70E provides guidelines for electrical safety workwear. ANSI Z49.1 covers general welding safety requirements.
TPP and ATPV testing measures how much thermal energy a fabric can withstand before causing second-degree burns. Higher numbers mean better protection.
Material | Heat Resistance | Durability | Comfort | Cost |
---|---|---|---|---|
Leather | Excellent | Excellent | Fair | High |
FR Cotton | Good | Good | Excellent | Medium |
Denim | Fair | Good | Good | Low |
CarbonX | Excellent | Excellent | Good | High |
Wool | Good | Fair | Good | Medium |
Inherent aramid fibers have flame resistance built into their molecular structure. When they hit flame, they char instead of burning, creating a protective barrier between the heat and your skin.
Chemical treatment involves applying flame-retardant chemicals to natural fibers. These chemicals make the fabric char and self-extinguish when exposed to flame. The key is that the char layer insulates the fabric underneath and protects you.
Here's the catch: chemical treatments can degrade over time and washing cycles. That's why following manufacturer care instructions matters so much.
This is where I've seen the most dangerous mistakes in my career. Polyester and nylon have absolutely no place in welding environments.
When synthetics melt, they form hot, sticky droplets that stick to your skin and keep burning. These melt-drip injuries are some of the worst burns you can get—they're difficult to treat and leave permanent scars.
Your safe fiber checklist should include 100% cotton for natural flame resistance, wool for the same reason, FR-treated natural fibers that have been properly certified, inherent FR synthetics like aramids, and leather for natural protection.
What you absolutely must avoid: polyester blends, nylon, acrylic, and any untreated synthetic. These materials will melt to your skin and cause injuries that could end your career.
Good welding apparel costs real money, so you want to get every bit of life out of it. But here's the thing—proper care isn't just about your wallet. It's about keeping the protective properties that literally keep your skin intact.
Following manufacturer wash instructions might seem like a pain, but those labels exist for a reason. FR treatments can break down with the wrong detergent or water temperature. Hot water might feel like it cleans better, but it can actually strip away the chemicals that keep you from becoming a human torch.
Air drying beats machine drying every single time. High heat from dryers doesn't just shrink your gear—it can degrade FR treatments and make natural fibers brittle.
Before you put on any piece of welding apparel, give it a quick once-over. Check for holes or tears in areas that take the most abuse—usually the chest, arms, and shoulders. Examine the seams where Kevlar stitching might be coming loose. Look for oil or grease stains that can actually make FR fabrics more flammable.
Know when to retire a piece of gear. If you can see through it, it's done. If the seams are failing in spots that protect vital areas, it's time to shop.
Smart welders know how to squeeze extra life out of quality gear. Patch kits using matching FR materials can save a jacket that just has a small tear. Apply patches to both sides for maximum strength—one patch is just a band-aid waiting to fail.
When seams give out, re-stitching with Kevlar thread creates repairs that are actually stronger than the original. Regular thread will melt under welding conditions, but Kevlar holds up to the abuse.
Many welders want custom logos on their gear, and that's fine as long as you use FR thread for the embroidery.
Sometimes the best improvements come from your own workshop. Adding leather elbow patches to cotton jackets creates armor in high-wear spots. These areas take a beating during long welding sessions, and a simple patch can double the life of your jacket.
Snap-on leather patches are genius for areas that see heavy spatter. You can remove and replace these protective patches without replacing the whole garment.
Hot environments call for creative solutions. Adding mesh panels under the arms or across the back improves airflow without compromising protection. Just make sure any mesh you add is made from FR materials.
Here's a trick that's saved me countless trips back to the truck: sewing in small magnetic strips (covered with FR fabric) creates convenient tool storage. Your electrode holder or small tools stay right where you need them without compromising safety.
The welding apparel industry is finally catching up with what we welders have been asking for all along—gear that actually works with us, not against us. After decades of making do with stiff, uncomfortable protection, we're seeing real innovation that makes a difference on the job.
The biggest game-changer we're seeing is lighter stretch FR blends that move like your favorite old work shirt but protect like heavy leather. These new fabrics combine aramid fibers with cotton in ways that give you the flexibility to reach overhead welds without feeling like you're wrestling your jacket.
Moisture-wicking liners are another breakthrough that's making long days more bearable. Instead of sweating through your shirt by 10 AM, these built-in systems pull moisture away from your skin and help regulate temperature. This isn't just about comfort—it's about safety. When you're not overheating, you make better decisions and stay more alert.
We're also seeing built-in hood systems that actually work with your helmet instead of fighting it. These integrate seamlessly with your welding helmet, protecting your neck and the back of your head without the bulk.
The push for workplace visibility has led to hi-vis reflective FR materials that meet both flame resistance and high-visibility standards in one garment. This is huge for industrial sites where you need to be seen by crane operators and heavy equipment while still staying protected from welding hazards.
While still in development, smart-sensor heat alerts could be the next big safety breakthrough. These systems would warn you when your gear is reaching dangerous temperatures—think of it as an early warning system for heat stress and potential gear failure.
More manufacturers are focusing on environmental considerations without sacrificing protection. This means developing FR treatments that are less harmful to produce and dispose of, plus creating materials that can be recycled at the end of their service life.
U.S.-made craftsmanship continues to lead the innovation charge because American manufacturers understand what real welders need. At Tentacle Tools, we see this commitment to quality and innovation every day, and we're proud to be part of the American manufacturing tradition that builds gear tough enough for the hardest jobs.
The key to smart welding apparel purchases is thinking beyond the price tag. Total cost of ownership includes how long the gear lasts, how often you need repairs, and whether it actually keeps you safe when things go sideways.
Bundle buying strategies can save serious money if you think it through. Buy multiple FR shirts so you can rotate them through the wash, but share the expensive leather jacket and specialized gear across your crew.
Warranty considerations matter more than most people realize. Quality manufacturers back their gear because they know it works.
The smartest approach is process matching—invest in premium gear for your main welding work, then use more economical options for occasional tasks.
After decades in the field and thousands of conversations with welders, we keep hearing the same questions about welding apparel. Let me share the answers that matter most for your safety and success.
The short answer is that your gear needs to meet OSHA 1910.252(b)(3) and ANSI Z49.1:2021 standards. These regulations aren't just bureaucratic paperwork—they're written in the blood of welders who got hurt using inadequate protection. The standards require that your protective clothing minimizes four critical risks: ignition, burning, spark trapping, and electric shock.
For most general welding work, gear meeting these basic standards will keep you safe. But if you're doing arc flash work or electrical maintenance, you'll need clothing that meets NFPA 70E standards with appropriate ATPV ratings.
Here's the practical advice: always verify that your gear meets the specific standards required for your work environment. Different job sites may have different requirements, and it's your responsibility to know what's needed.
This question hits close to home because I've seen too many welders try to squeeze extra life out of gear that should have been retired months ago.
Replace your welding apparel immediately when you notice holes, tears, seam failure, or loss of FR properties. No exceptions. A small hole might seem harmless, but it's an invitation for sparks to reach your skin.
For daily-use garments, expect 6-12 months of service life depending on your work conditions and how well you care for the gear. Pipeline welders working in harsh conditions might need to replace gear more frequently, while shop welders in controlled environments can often get longer life from their apparel.
The key is inspecting your gear before each use. Look for worn spots, check seams for loose stitching, and test that FR properties are still working. If fabric continues burning after you remove the flame source, it's time for replacement.
FR treatments can degrade over time, especially with frequent washing. Even if the garment looks fine, the protective chemistry might be compromised. When in doubt, replace it—your skin is worth more than saving a few dollars on gear.
Yes, and it's about time the industry caught up with reality. Women welders deserve gear that fits properly and provides the same level of protection as men's gear.
Many manufacturers now offer women-specific welding apparel with proper fit through the torso, arms, and shoulders. These aren't just smaller versions of men's gear—they're designed with different proportions that account for how women's bodies are shaped.
Proper fit is crucial for safety. Loose clothing can catch sparks and create hazards, while tight clothing may not provide adequate coverage or allow proper movement. Women-specific cuts solve these problems by providing protection without excess bulk.
The protection standards are identical regardless of who's wearing the gear. Women's welding apparel meets the same OSHA and ANSI requirements as men's gear—the only difference is the fit and comfort.
After two decades in the oil and gas fields, I've seen how the right welding apparel can mean the difference between going home safe and facing a life-changing injury. Your protective gear isn't just clothing—it's your armor against temperatures hotter than the sun's surface and hazards that can end careers in an instant.
The choice is yours, but it's not one to take lightly. Quality welding apparel that meets OSHA standards and fits properly will protect you through countless jobs and challenging conditions. Cheap gear that melts, tears, or fails when you need it most isn't saving you money—it's putting your livelihood and your life at risk.
At Tentacle Tools, we understand what it takes to build America. Our American-made tools are designed by welders who've been in your boots, who know what real protection means when sparks are flying and deadlines are tight. But we're not just about manufacturing—we're about supporting the entire skilled trades community.
That's why we're proud to offer our dedicated job board that connects welders, fitters, and tradespeople with opportunities across the United States. Whether you're looking for your next pipeline job or seeking skilled professionals for your crew, we're here to help build the connections that keep America running.
Your safety gear is an investment in every future paycheck, every family dinner you'll make it home for, and every project you'll complete safely. Choose gear that matches your work demands, maintain it properly, and never let anyone pressure you to cut corners on protection.
Stay safe out there, and remember—the tools and gear that built this country are still building it today, one weld at a time.
Explore insights, tips, and trends in tech and productivity!