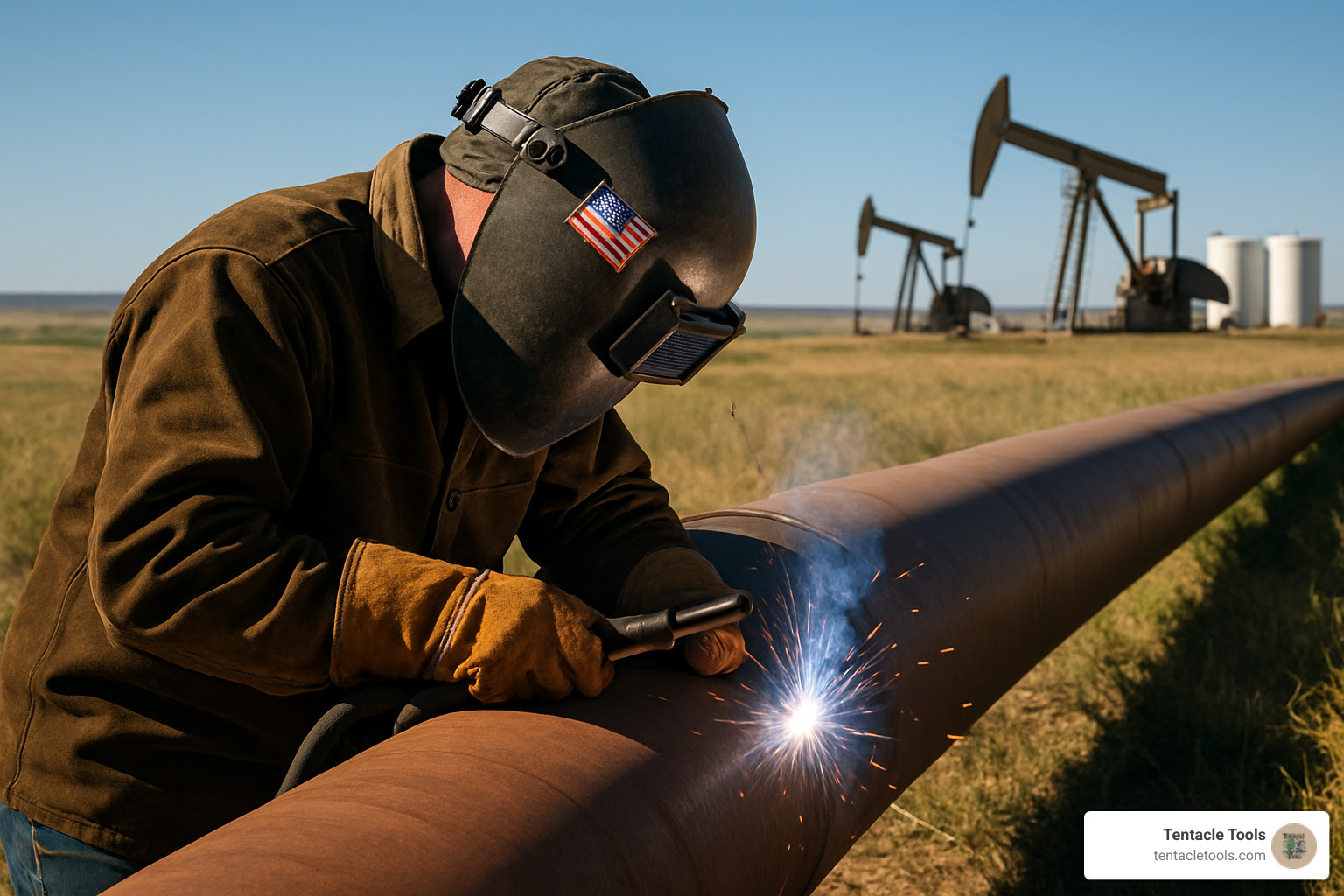
Master Oil & Gas Industry Welding with our guide—techniques, safety, codes, automation, and tips for better reliability and efficiency.
Oil & Gas Industry Welding is the backbone of America's energy infrastructure, joining millions of miles of pipelines, offshore platforms, and refinery systems that deliver fuel to power our economy. Here's what you need to know:
Key Applications:- Upstream: Drilling rigs, wellheads, and gathering lines- Midstream: Long-distance pipelines and storage tanks
- Downstream: Refineries, petrochemical plants, and distribution systems
Common Welding Methods:- SMAW (Stick): Most versatile for field conditions- GMAW (MIG): Fast production welding- GTAW (TIG): Precision work on critical joints- FCAW: Wind-resistant outdoor welding- SAW: High-volume pipeline construction
Critical Requirements:- Withstand pressures up to 1,200 PSI- Operate in extreme temperatures and harsh environments- Meet strict API, ASME, and ISO standards- Pass rigorous NDT inspection requirements
The oil and gas industry was responsible for 54.7% of global energy consumption in 2023, with the United States maintaining 2.8 million miles of pipelines—all requiring extensive welding for installation and maintenance.
I'm William "Stick" Mank, a second-generation welder with over 20 years of hands-on experience in Oil & Gas Industry Welding, from pipeline construction to offshore platform repairs. Through this guide, I'll share the real-world knowledge you need to understand how welding keeps America's energy flowing safely and efficiently.
Common Oil & Gas Industry Welding vocab:- oil and gas jobs- pipeline welding inspection services oil and gas industry
Before the first drop of oil flows through a pipeline, welders have already laid the foundation for America's energy security. Structural integrity depends entirely on metallurgical bonding that can withstand decades of service under extreme conditions. A typical drill pipe string extends 3-4 miles underground, with sections joined by welds that must handle enormous torque and tension.
Production efficiency also hinges on welding quality. When a weld fails on a major pipeline or refinery vessel, the resulting downtime can cost operators thousands of dollars per hour. That's why the industry has acceptd automation and advanced welding processes—because consistent, high-quality welds directly translate to reliable energy production.
When you look at America's energy infrastructure, you're seeing the result of decades of Oil & Gas Industry Welding that spans an incredibly complex value chain. From drilling for oil to gasoline reaching your local station, welders are the unsung heroes making it all possible.
The challenges we face go way beyond typical fabrication. We're dealing with pressure and temperature extremes that would destroy most materials. Picture a pipeline carrying natural gas at 1,200 PSI through the Arizona desert at 120°F, or an offshore platform in the North Sea withstanding hurricane-force winds.
Carbon steel remains our bread and butter for most applications—it's reliable, cost-effective, and proven. When corrosion becomes a threat, we turn to duplex and super duplex stainless steels. For the really tough jobs—sour gas service or high-temperature refinery equipment—nickel alloys become essential, often requiring post-weld heat treatment (PWHT).
Welding Process | Best For | Advantages | Limitations |
---|---|---|---|
SMAW (Stick) | Field repairs, all positions | Versatile, wind-resistant | Slower deposition rates |
GMAW (MIG) | Production welding, automation | Fast, clean | Requires shielding gas |
GTAW (TIG) | Root passes, critical joints | Precise control, clean welds | Slower, requires skill |
FCAW | Outdoor construction | Wind-resistant, fast | Can produce more spatter |
SAW | Pipeline construction | High deposition, automated | Flat/horizontal positions only |
Upstream exploration and production presents unique challenges. Offshore drilling rigs must handle 40-foot waves and hurricane winds while resisting saltwater corrosion. Onshore drilling faces extreme temperatures—from Alaska where we preheat base metal to 65-70°F, to desert heat above 120°F.
Midstream transmission pipelines are engineering marvels transporting oil and gas across thousands of miles. Orbital welding has revolutionized root passes, providing consistency manual welding can't match. Storage tanks holding millions of barrels require perfect longitudinal and circumferential welds.
Downstream refineries transform crude oil through processes involving extreme heat, pressure, and corrosive chemicals. Desulphurization reactors, hydrocracking units, and distillation columns each present unique welding challenges requiring specialized techniques.
The codes governing our work represent decades of accumulated wisdom. API 1104 sets pipeline welding standards, ASME Section IX governs pressure vessel procedures, and ISO 3834 provides quality management frameworks. These aren't bureaucratic red tape—they're what keeps our energy infrastructure safe and creates a common language for welders, engineers, and inspectors worldwide.
When you're working in Oil & Gas Industry Welding, choosing the right technique can mean the difference between a smooth job and a nightmare. I've spent two decades figuring out which process works best for each situation.
Shielded Metal Arc Welding (SMAW) is the old reliable of our industry. When I'm on a pipeline job with wind howling and weather changing, stick welding gets the job done. You don't need fancy equipment or gas bottles—just a good electrode and steady hands. It's not the fastest process, but when conditions get tough, stick welding keeps working.
Gas Metal Arc Welding (GMAW) is where you go when speed matters. MIG welding can lay down metal fast, making it perfect for long-seam welds on storage tanks. But GMAW hates wind—try running MIG outdoors without wind protection, and you'll get porosity that'll make inspectors shake their heads.
Gas Tungsten Arc Welding (GTAW) is the precision tool in our toolkit. When I need a perfect root pass or I'm working with stainless steel in a refinery, TIG welding is the only way to go. It's slower, but the quality is best. The clean welds you get with TIG are worth the extra time, especially in corrosive environments.
Flux-Cored Arc Welding (FCAW) gives you the best of both worlds—the speed of MIG with the wind resistance of stick. The flux core protects the weld from inside, so you can work outdoors without worrying about every breeze. I particularly love FCAW for coastal work with salt air and unpredictable weather.
Hyperbaric welding is like science fiction—creating a dry bubble around underwater work areas to repair pipelines 200 feet down when shutting down the system isn't an option.
Orbital welding takes the human element out of the equation in a good way. These automated systems produce root passes so consistent that every weld looks identical. For large pipeline projects with thousands of joints, orbital welding ensures quality while keeping schedules on track.
Electroslag welding handles really thick materials. When dealing with steel over 2 inches thick, ESW can weld it in a single pass. The scientific research on friction welding in drill pipe shows how critical these specialized processes are for drilling miles underground.
Friction welding creates bonds stronger than the base metal—essential for drill pipe connections facing enormous torque and stress.
Choosing the right welding process depends on material thickness, weld position, environmental conditions, and cost considerations. Thin-wall tubing needs precision, while heavy-wall pipe needs deposition rate. Overhead welding eliminates some processes, while flat position opens all options. High winds rule out GMAW, and offshore work demands processes that handle movement and salt spray.
The key is matching the process to job requirements, not just going with what you know best. Every technique in Oil & Gas Industry Welding has its place—you just need to know when and where to use each one.
When you're working with Oil & Gas Industry Welding, safety isn't just another checkbox—it's what keeps you going home every night. Our industry combines dangerous elements: intense heat, explosive materials, and high-pressure systems that don't forgive mistakes.
Welding burns are the most common injury. Arc eye—that sand-in-your-eyes feeling—happens when you think you can get away with a quick tack without proper eye protection. UV radiation burns your corneas faster than you can blink. Molten metal spatter reaches 6,000°F and finds every gap in your PPE.
Toxic gases and fumes are silent killers. Welding stainless steel creates chromium and nickel oxides that seriously damage lungs. Add ozone, nitrogen oxides, and carbon monoxide, and you've got a dangerous cocktail. These fumes build up in confined spaces—I've seen welders pass out in tanks because they thought they could tough it out without proper ventilation.
Electrical hazards become more dangerous around flammable materials. Arc welding operates at high voltages, and in oil and gas environments, everything seems wet or covered in conductive substances.
After two decades, I've learned comfort and protection go hand in hand. Leather gloves that fit properly give you dexterity while protecting from heat and spatter. Fire-resistant clothing isn't just about OSHA requirements—it's about staying alive when things go wrong. Respirators become critical when welding beyond basic carbon steel.
Gas monitors detect hydrogen sulfide, methane, and other hazards common in oil and gas operations. Proper ventilation systems move fumes away from your breathing zone. Hot work permits ensure everyone knows welding is happening with proper fire watch procedures in place.
In Oil & Gas Industry Welding, quality assurance prevents disasters. Radiographic testing shoots X-rays through welds to find internal defects. Ultrasonic inspection uses sound waves to measure penetration and detect cracks. Magnetic particle testing reveals surface defects that could grow under pressure cycling.
Every weld procedure specification must be qualified through destructive testing, and every welder certified for each process and position. Standards like API 1104, ASME Section IX, and OSHA 1910.252 aren't red tape—they're written from hard-learned lessons. The global energy mix is changing, but oil and gas remain critical, making our welding work more important than ever.
The future of Oil & Gas Industry Welding is being shaped by automation, advanced inspection technologies, and innovative training methods.
I've watched automation transform our industry over two decades. Robotic welders and spool welding robots now handle repetitive, high-volume work that used to require armies of welders. These systems produce consistent, high-quality welds with minimal human intervention.
Column and boom manipulators have revolutionized large-diameter pipe welding. Instead of welders contorting into uncomfortable positions, these systems allow precise positioning while keeping operators safe and comfortable. Weld positioners rotate work pieces to maintain optimal angles, dramatically improving quality and comfort.
The productivity gains are substantial. Automated systems operate continuously without fatigue, producing consistent welds with minimal defects. Data logging provides complete documentation of welding parameters, creating permanent records for quality assurance and regulatory compliance.
But worker safety improvements may be more important than productivity gains. Automation reduces human exposure to hazardous environments, from confined spaces to offshore platforms in severe weather.
Laser-hybrid welding combines laser precision with arc welding's gap-bridging capability. Cold-spray technology applies corrosion-resistant coatings without heat input that might affect base metal properties.
Smart sensors provide real-time feedback on arc characteristics and heat input, enabling predictive maintenance programs. Digital twin simulation allows engineers to model complex welding scenarios before beginning actual work. AI vision systems detect weld defects in real-time, catching problems before they become expensive repairs.
The skills gap continues challenging our industry, but new training methods help bridge it. Virtual training programs offer immersive learning experiences supplementing traditional hands-on training. Modern welders need to understand duplex additive filler materials and sustainability metrics that weren't considerations a generation ago.
At Tentacle Tools, we support the skilled trades community through our dedicated job board connecting welders with opportunities across the oil and gas industry. Our goal is equipping tradesmen with both tools and career opportunities they deserve.
The future of Oil & Gas Industry Welding isn't about replacing welders—it's about empowering them with better tools, safer working conditions, and more rewarding careers.
After two decades in Oil & Gas Industry Welding, I get asked the same questions repeatedly. Here are the answers that matter most.
Shielded Metal Arc Welding (SMAW) wins for pipeline work. When you're welding with 20-mph winds and no shelter, stick welding just works. The flux coating protects the weld pool without external shielding gas that wind can blow away.
For high-production pipeline construction, Submerged Arc Welding (SAW) takes over after the root pass. SAW lays down metal fast with excellent penetration, perfect for fill and cap passes on long pipeline runs.
Offshore welding means dealing with salt spray that eats through regular steel. Everything needs corrosion resistance, from base materials to welding consumables. The platform never stops moving, making gas-shielded processes tricky. That's why Flux-Cored Arc Welding (FCAW) works well offshore—flux provides protection from within.
Onshore operations give you more equipment options and easier access when problems arise. But don't think it's easier—I've welded in North Dakota winters where we preheated everything to 70°F, and desert work at 120°F brings its own challenges.
API 1104 is your bible for pipeline welding, covering everything from procedures to inspection requirements. ASME Section IX governs pressure vessel welding procedures and welder qualifications. ISO 3834 provides quality management frameworks ensuring proper procedures and documentation. These standards work together like a safety net, each covering different aspects but all pointing toward reliable welds that keep America's energy infrastructure running safely for decades.
Oil & Gas Industry Welding keeps America's lights on, cars running, and economy moving. Every time you flip a switch or fill up your tank, you're relying on skilled welders who built and maintain the 2.8 million miles of pipelines, offshore platforms, and refineries that deliver energy to your door.
This isn't just about joining metal—it's about national security, economic stability, and the hard work that built this country. From welders making hyperbaric repairs 200 feet underwater to crews building pipeline spools in Texas heat, these professionals understand their work matters in ways most people never see.
The industry keeps pushing forward with new technologies and better safety practices. Robotic welders are making dangerous jobs safer. Advanced materials last longer in harsh environments. But skilled hands and sharp minds still make the difference between a job done right and catastrophic failure.
At Tentacle Tools, we get it because we've been there. Our founder is a double-time welder who knows what it's like to work 12-hour shifts in challenging conditions. That's why we design American-made specialty welding tools that solve real problems for real welders.
We're not just selling tools. Our job board connects welders with opportunities across the oil and gas industry because we believe skilled tradespeople deserve both quality equipment and quality careers. When you succeed, America succeeds.
The future of Oil & Gas Industry Welding will bring new challenges as energy demands grow and technology advances. But one thing won't change—the need for welders who take pride in their craft and understand that every bead they lay helps power the greatest country on earth.
Ready to see what tools built by welders, for welders can do for your work? Check out our catalog and find equipment that embodies the same hard work, grit, and patriotism that keeps America's energy flowing.
Explore insights, tips, and trends in tech and productivity!