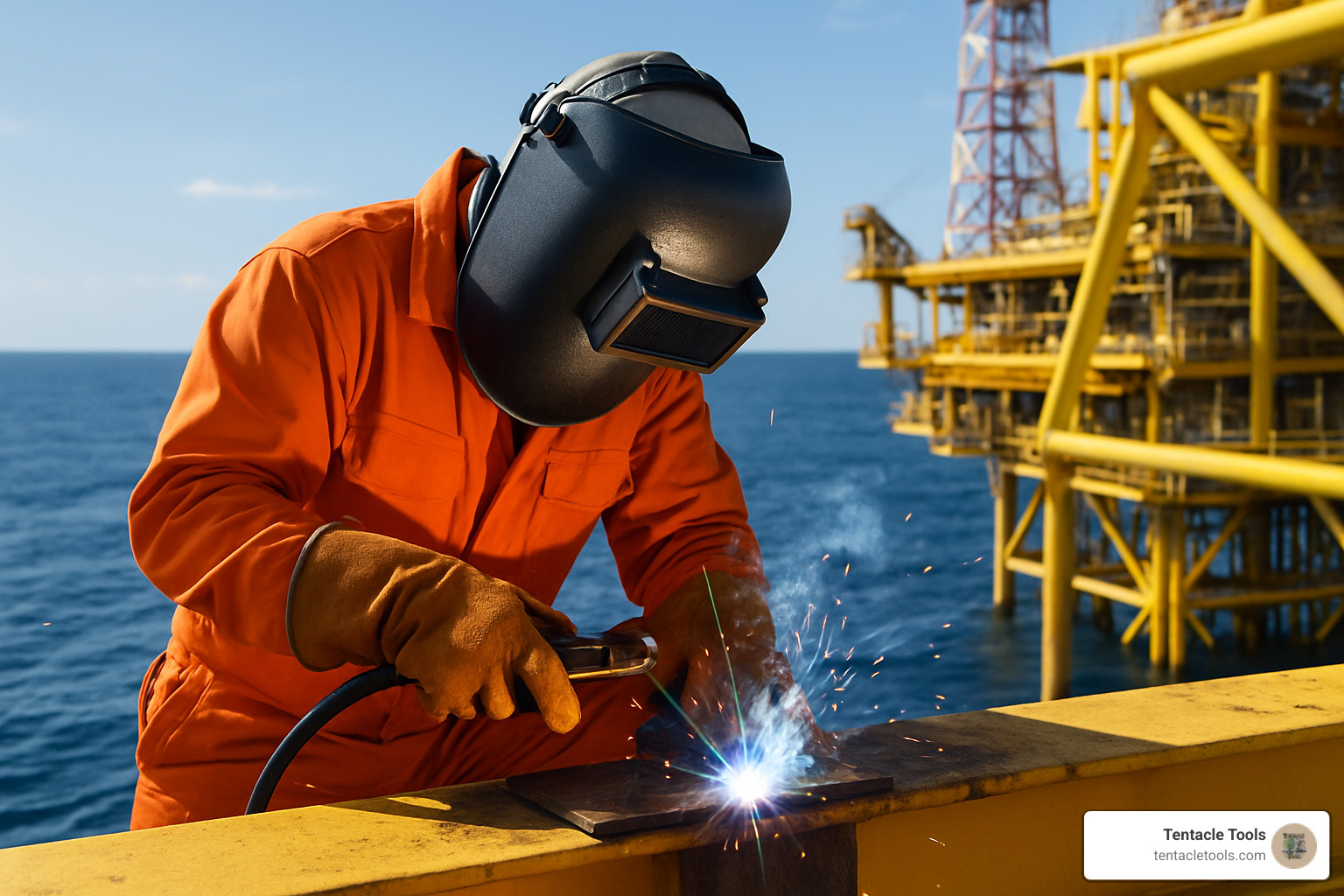
Discover how to become an off shore welder, from training to top careers, pay, and military transition tips for the maritime industry.
An off shore welder is a specialized tradesperson who performs welding operations on offshore installations such as oil rigs, platforms, pipelines, and wind farms. If you're considering this career path, here's what you need to know:
Offshore Welder Overview | Details |
---|---|
Average Salary | $49,140 (US), £67,500 (UK) |
Work Schedule | 2-6 week rotations (equal time off) |
Required Certifications | BOSIET, HUET, 6G welding code, offshore medical |
Common Processes | SMAW, GTAW, FCAW |
Job Growth | 7% projected by 2028 |
The open ocean is calling, and for skilled welders looking to lift both their career and income, offshore welding represents one of the most challenging and rewarding paths in the trade.
Working as an off shore welder means trading the predictability of land-based jobs for a lifestyle that's anything but ordinary. Instead of commuting to the same shop each morning, you might find yourself boarding a helicopter bound for a drilling platform hundreds of miles from shore, carrying specialized equipment designed to withstand corrosive saltwater and extreme weather conditions.
"It's not an overstatement to say that environmental conditions on offshore rigs are brutal," notes one industry veteran. "But the satisfaction of completing critical repairs in these conditions—knowing that people's safety depends on your work—is best in the welding world."
Unlike typical welding positions, offshore work often operates on rotation schedules—commonly 2 to 6 weeks on the platform followed by an equal period at home. During your "on" weeks, you'll work 12-hour shifts, seven days straight, living in close quarters with your crew. It's demanding work, but the extended time off and significantly higher pay compensate for the intensity.
Most offshore facilities station only one or two welders at a time, making you responsible for all welding requirements that arise—from emergency repairs to routine maintenance and new construction. You'll need to master multiple welding processes and be comfortable working with everything from carbon steel to exotic alloys like super duplex stainless and titanium.
For those transitioning from military service, the structured environment, safety protocols, and intense work periods often feel familiar, making veterans particularly well-suited to the offshore lifestyle.
When you become an off shore welder, you're not just taking on a job – you're embracing a whole different lifestyle. These specialized tradespeople practice their craft miles from shore on oil rigs, wind farms, and maritime installations, often in conditions that would make land-based welders think twice.
Picture yourself climbing out of a helicopter onto a swaying platform surrounded by nothing but open ocean, knowing your skills will be tested by saltwater corrosion, howling winds, and the constant motion of the sea. It's not your average welding gig, that's for sure!
Off shore welders tackle their work as part of tight-knit crews where everyone depends on each other. When you're hundreds of miles from the nearest hardware store, you can't just run out for a new part – you become a problem-solver who makes things work with what you've got.
"Out here, you're not just a welder – you're the welder," explains Jay, a 15-year platform veteran. "When something breaks at 2 AM and production is halted, all eyes turn to you. That pressure isn't for everyone, but some of us thrive on it."
Every weld you make offshore must meet rigorous international standards with complete documentation and traceability. When your work could be the difference between safety and catastrophe, there's zero room for cutting corners.
The daily life of an off shore welder is remarkably diverse. One day you might be performing routine maintenance on corroded handrails, and the next you could be fabricating a custom replacement part for critical equipment that can't wait for the next supply boat.
Your responsibilities extend far beyond just laying beads. You'll find yourself conducting emergency repairs when equipment fails unexpectedly, installing new components during facility upgrades, and carefully documenting every weld for quality assurance.
Many offshore welders describe the satisfaction that comes from solving problems in challenging environments. "There's nothing like finishing a complex pipe repair in a tight space during rough seas, knowing that without your skills, the whole operation might have been shut down," says Mike, who's worked in the Gulf of Mexico for over a decade.
The offshore environment demands mastery of several specialized welding disciplines:
Topside welding takes place above the waterline on the platform itself. You'll primarily use SMAW (stick) and FCAW (flux-core) processes, often working inside pressurized habitats that keep explosive gases at bay while you work near production equipment.
When repairs are needed below the surface, hyperbaric dry welding comes into play. This technique involves creating a pressurized chamber around the underwater work area, allowing for high-quality welds comparable to those done topside.
For emergency situations where time is critical, wet welding becomes necessary. Using specialized waterproof equipment and electrodes, you'll weld directly underwater – a challenging skill that separates the elite from the average offshore welder.
Pipeline welding offshore often combines precision GTAW (TIG) root passes with efficient FCAW fill passes to join sections of the critical pipelines that transport oil and gas. The stakes are incredibly high, with each joint requiring flawless execution.
The platforms themselves require constant structural welding to maintain their integrity against the relentless ocean environment. This work typically relies on FCAW for its excellent mechanical properties and ability to deposit material quickly in structural applications.
Your skills as an off shore welder open doors to several maritime industries:
The oil and gas sector remains the largest employer, with fixed platforms and tension-leg platforms requiring continuous maintenance and periodic major modifications. These massive structures are essentially small cities at sea, with welding needs that never end.
FPSOs (Floating Production, Storage and Offloading vessels) combine maritime vessel elements with production equipment, creating unique welding challenges that require versatility and adaptability.
The offshore wind industry is experiencing explosive growth, with thousands of turbines being installed on welded foundations. "I've watched guys who spent 20 years welding on oil platforms transition to wind farms," notes a project manager. "The core skills transfer perfectly, and many welders appreciate contributing to renewable energy."
Many offshore careers begin in shipyards and vessel repair facilities. While technically not "offshore," these environments provide valuable experience with maritime-grade materials and standards that serve as stepping stones to platform work.
The vast networks of subsea pipelines that transport oil and gas across ocean floors require specialized welding techniques for installation and repair, creating another niche for skilled offshore welders.
As energy needs evolve, so do the opportunities for off shore welders – from maintaining aging infrastructure to building the renewable energy platforms of tomorrow. The ocean may be demanding, but for those with the right skills and temperament, it offers a career unlike any other.
Becoming an off shore welder requires a substantial investment in training and certification. The high-risk environment demands rigorous preparation and formal qualifications that go well beyond basic welding skills.
Before you can even set foot on an offshore installation, you'll need to earn your stripes with several essential certifications. Think of your BOSIET (Basic Offshore Safety Induction and Emergency Training) as your offshore passport – without it, you simply won't be getting on that helicopter. This comprehensive course covers everything from helicopter safety and sea survival to firefighting and first aid.
Most offshore workers still remember their first HUET (Helicopter Underwater Escape Training) experience with a mix of dread and pride. This intense training – often included in your BOSIET – simulates what happens when a helicopter ditches in open water. You'll practice escaping from a submerged helicopter simulator, sometimes while it's being rolled upside down. As one trainer reassuringly puts it, "Even people who can't swim can complete HUET with attentive instructors."
Rounding out your basic qualifications, you'll need MIST (Minimum Industry Safety Training) certification covering essential safety protocols, and a valid offshore medical certificate that verifies you're physically fit for the demands of the job. This thorough examination checks everything from your cardiovascular health to vision, hearing, and mobility.
Of course, your actual welding credentials are equally crucial. "You should also be coded to 6G (6GR)," advises one industry veteran. "These are your ticket to the dance – without them, your application won't get a second look." These all-position pipe certifications demonstrate you can handle the complex welding scenarios you'll encounter offshore.
For more information about specialized training programs that can help you qualify, check out our blog on training pathways.
Beyond the basic offshore access requirements, successful off shore welders need a robust toolkit of specialized skills.
Your welding process mastery needs to be versatile. You'll rely heavily on stick welding (SMAW) for general repairs and structural work, especially in windy conditions where shielding gases might be blown away. TIG welding (GTAW) skills are essential for precision work, particularly on root passes and thin materials where quality standards are unforgiving. And flux-cored (FCAW) welding will be your go-to for high-deposition structural work when you need to lay down a lot of metal quickly.
Material knowledge sets the professionals apart from the rookies. While carbon steel will make up the bulk of your work, you'll need experience with specialty metals like austenitic stainless steels, duplex and super duplex stainless steels, nickel-based alloys, copper-nickel, and occasionally even titanium.
Your technical skills need to extend beyond just running beads. Blueprint reading is non-negotiable – you'll often be the only welder on site interpreting complex drawings. A working knowledge of non-destructive testing helps you understand how your welds will be evaluated. Familiarity with welding procedure specifications (WPS) ensures you're executing work to exact standards. And proficiency with permit-to-work systems and confined space entry procedures keeps you safe in hazardous environments.
If underwater welding is your goal, add commercial diving certification, AWS D3.6 underwater welding certification, CSWIP 3.0 underwater inspection qualification, and IMCA-recognized diving certification to your shopping list. For those working at heights on platforms or wind turbines, IRATA or equivalent rope access certification is increasingly valuable.
The offshore industry takes safety deadly seriously, and for good reason. Your safety training will be extensive and challenging.
Helicopter escape drills will push you outside your comfort zone as you practice emergency exits from helicopters, including underwater egress while wearing a survival suit. Advanced firefighting training teaches you to combat different classes of fires in confined industrial settings where escape options are limited. Sea survival courses prepare you for the unthinkable – surviving in open water after an evacuation, including life raft deployment and proper use of personal survival equipment.
The medical requirements for offshore work catch many aspiring welders by surprise. "The offshore medical is comprehensive," explains a safety trainer. "You need to demonstrate not just absence of illness, but positive fitness for the demanding offshore environment."
Your BMI will need to fall within acceptable ranges. Your blood pressure and cardiovascular health will be carefully evaluated – heart problems are a serious concern when you're hours away from the nearest hospital. Vision and hearing tests ensure you can perceive hazards in a noisy industrial environment. Musculoskeletal assessments confirm you can handle the physical demands of climbing, lifting, and working in awkward positions. And comprehensive drug and alcohol screening is standard, along with psychological evaluation to ensure you can handle the isolation and pressure.
In offshore welding, quality isn't just about pride in your work – it's a matter of life and death. Off shore welders operate in an environment where weld failures can have catastrophic consequences, so rigorous quality control processes are part of daily life.
Documentation becomes your constant companion. You'll work with detailed Welding Procedure Specifications (WPS) that specify exactly how each weld must be executed. Procedure Qualification Records (PQR) validate that these procedures produce acceptable results. Your personal qualifications and test results will be carefully documented. Detailed weld maps and logs track every joint you complete, and material traceability records follow each piece of metal from manufacture to installation.
"Full traceability per weld joint is maintained to meet compliance requirements," notes a quality control manager. "This documentation provides peace of mind in hectic offshore environments."
Your welds will face multiple inspection methods: visual inspection (VT) for surface defects, magnetic particle testing (MT) to find near-surface cracks, dye penetrant testing (PT) for non-magnetic materials, radiographic testing (RT) for internal defects, and ultrasonic testing (UT) for thick sections.
Quality control procedures differ significantly between topside and subsea environments:
Aspect | Topside QC | Subsea QC |
---|---|---|
Visual Inspection | Immediate, direct | ROV camera or diver |
Documentation | Digital systems | Specialized waterproof |
NDT Methods | Full range available | Limited by environment |
Acceptance Criteria | Standard codes | Modified for environment |
Repair Options | Multiple processes | Limited techniques |
The path to becoming an off shore welder isn't easy, but the investment in qualifications and training pays off. Each certification you earn not only makes you more employable but better equipped to work safely and effectively in one of the world's most challenging environments.
The equipment used by off shore welders must withstand extreme conditions while delivering consistent performance. Unlike land-based welding shops, offshore environments demand specialized gear engineered for reliability in corrosive, damp, and often unstable conditions.
Welding power sources for offshore use can offer up to 1500 amps and typically feature:
"When working on an offshore oil rig, you want safety, integrity, durability, reliability, and versatility as prime pillars of your welding equipment," emphasizes an equipment specialist.
For more detailed information about specialized offshore welding equipment, check out Lincoln Electric's offshore welding solutions guide.
The personal protective equipment (PPE) required for off shore welders goes beyond standard welding gear, reflecting the additional hazards present in maritime environments:
"Your PPE is your last line of defense in an environment where even minor incidents can escalate quickly," warns a safety coordinator. "Offshore welders learn to be meticulous about their protective gear."
While there are more than 100 welding methods available, off shore welders primarily use a select few processes best suited to maritime conditions:
SMAW (Shielded Metal Arc Welding): The workhorse process offshore, valued for its portability and versatility in all positions. Particularly useful for:
GTAW (Gas Tungsten Arc Welding): Essential for:
FCAW (Flux-Cored Arc Welding): Preferred for:
SAW (Submerged Arc Welding): Used in specialized applications:
The materials commonly welded offshore include:
"Welding CRA materials offshore requires exceptional skill," notes a veteran welder. "You're often performing GTAW root passes in restrictive positions with little room for error, knowing that a defect could lead to corrosion failure in critical systems."
The working environment for off shore welders presents unique challenges:
Physical conditions:
Work arrangements:
"Working offshore isn't just about welding skill—it's about mental toughness," explains an experienced offshore welder. "You need to function at a high level while dealing with isolation, confined living, and the constant awareness that you're surrounded by potential hazards."
Hurricane seasons can also disrupt work patterns, with platforms sometimes evacuated on short notice. As one welder recounts, "Hurricane Gustav damaged more than 130 offshore platforms in 2008. After such events, welders are in high demand for emergency repairs."
The financial rewards of becoming an off shore welder are substantial, especially compared to land-based positions. The challenging nature of offshore work commands premium compensation that reflects both the skills required and the lifestyle sacrifices made.
The average salary for an off shore welder in the US hovers around $49,140, while UK welders typically earn about £67,500. But don't let these figures fool you – they often don't include the overtime, bonuses, and specialty pay that can dramatically increase your take-home.
Most newcomers to offshore welding start around $41,000, but experienced professionals regularly break into six-figure territory. If you specialize in underwater welding, you'll also benefit from "depth pay" – an additional $1-4 per foot of depth – which can significantly fatten your paycheck on deeper projects.
The offshore lifestyle isn't for everyone, but it offers unique advantages for those who accept it.
On the plus side, the pay is significantly better than what you'd earn doing similar work onshore. The rotation schedule gives you extended blocks of time off – imagine having 2-4 weeks completely free rather than just weekends. Many welders use this time to pursue hobbies, travel, or simply be fully present with family.
The travel opportunities can be incredible too. Depending on your employer, you might find yourself working in the Gulf of Mexico one month and off the coast of West Africa the next. Many welders value the strong camaraderie that develops when working closely with a small crew in isolated conditions.
"When you're 200 miles offshore with the same 12 guys for a month, you either become brothers or enemies," jokes one veteran welder. "Thankfully, it's usually the former."
Of course, there are downsides. Family separation is the hardest part for most offshore welders. Missing birthdays, anniversaries, and everyday moments can strain relationships. The physical demands are intense – 12-hour shifts in awkward positions, often in extreme heat or cold.
Living conditions can be cramped, with shared quarters and limited privacy. The safety risks are higher than onshore welding, and mental challenges like isolation and monotony between shifts can wear on you. And when bad weather hits, you might find your rotation unexpectedly extended or cut short with little notice.
As one off shore welder put it: "The money's great, but you're trading time for dollars. You have to decide if that trade makes sense for your life."
One of the best aspects of offshore welding is the clear path for advancement. With experience and additional certifications, you can move up to positions that offer more responsibility, better pay, and often less physical strain.
Many start as general off shore welders and progress to lead welder positions, supervising other welders and coordinating activities. From there, becoming a welding foreman means managing entire crews and interfacing with other departments.
Many experienced welders leverage their knowledge to transition into QC inspection. Your intimate understanding of what makes a good weld becomes invaluable when verifying others' work. This role typically involves less physical strain while maintaining competitive compensation.
Other popular advancement paths include becoming an NDT technician specializing in non-destructive testing, moving into welding engineering to develop procedures and solve technical challenges, advancing to project management, or even transitioning to technical sales representing equipment manufacturers.
"After 15 years of offshore welding, my knees weren't what they used to be," shares one former welder. "Moving into inspection was the perfect next step – I still use my welding knowledge every day, but now I'm checking welds instead of making them."
The future looks bright for off shore welders, with the U.S. Bureau of Labor Statistics projecting 7% growth for underwater welding and commercial diving jobs by 2028.
Several factors are driving this demand. The energy transition is creating opportunities in new sectors – while traditional oil and gas may see fluctuations, offshore wind farm construction is booming globally. These massive structures require skilled welders during both installation and maintenance.
Aging infrastructure is another key factor. Many offshore platforms are exceeding their original design life and require increasing maintenance and reinforcement – work that demands skilled welders. Similarly, decommissioning projects for older platforms create specialized welding needs for safe dismantling.
New subsea developments continue to be installed across various industries, creating fresh demand. And with many experienced welders reaching retirement age, a skilled labor shortage is opening doors for newcomers.
"The offshore welding market isn't disappearing – it's evolving," explains an industry analyst. "The welders who thrive will be those who stay adaptable and continuously upgrade their skills to work across different offshore sectors."
For those willing to accept the unique lifestyle and challenges, offshore welding offers financial rewards and career opportunities that few other trades can match. And when you're ready to find your next position, resources like the Tentacle Tools job board can connect you with employers seeking skilled tradespeople across the country.
Breaking into offshore welding isn't always smooth sailing, but with the right approach, you can steer your way into this rewarding career path – even without prior maritime experience. What matters most is showcasing both your technical welding skills and the personal qualities that make you suited for offshore life.
"It's more who you know than what you know in getting offshore jobs," a veteran welder once told me. This insider perspective highlights something important – networking matters in this tight-knit industry. But don't worry if your contact list is looking a bit thin right now. Proper preparation can help you overcome this hurdle.
To make yourself a standout candidate, consider investing in essential certifications like BOSIET, HUET, and your offshore medical exam. Most employers won't cover these costs for first-timers, so self-funding these credentials shows you're serious about your offshore career. It's also smart to upgrade your welding qualifications – that 6G certification in multiple processes (especially SMAW and GTAW) will put you miles ahead of the competition.
When crafting your resume, make it offshore-specific. Highlight your safety consciousness, experience working in confined spaces, and familiarity with relevant materials and processes. They're not just hiring a welder – they're hiring someone who can handle the unique offshore environment.
"My resume for land jobs and offshore jobs looked completely different," shares Mike, who's been welding offshore for 15 years. "For offshore, I emphasized my experience with high-pressure pipe and my ability to work long shifts without supervision. That's what caught their attention."
Don't overlook specialized job boards, including Tentacle Tools' dedicated welding job board that connects skilled tradespeople with employers across the industry. Building relationships with recruiters who specialize in maritime and energy sector placements can also open doors that might otherwise remain closed.
Be flexible about your first assignment. That initial offshore job might be short-term or less glamorous than you hoped, but it establishes crucial experience that makes the next job easier to land. Every day offshore is another day of proof that you can handle the lifestyle.
If you're starting with zero offshore experience, don't get discouraged. Several pathways can help bridge that experience gap:
Shipyard experience is golden. Working in shipbuilding or repair provides relevant skills and introduces you to people connected to offshore operations. Similarly, dockyard maintenance supporting offshore vessel repairs during port calls can build valuable connections with offshore personnel.
Consider shutdown projects – those short-term maintenance gigs when facilities are offline often have less stringent experience requirements. Adding rope access certification (like IRATA) to your skillset makes you immediately more valuable for those hard-to-reach areas on platforms.
"I started in a shipyard welding pipe for three years before getting my first two-week offshore hitch," shares James, now a lead welder on a North Sea platform. "That first short job led to more calls because I'd proven I could handle the environment and produce quality work under pressure. The rest is history."
Specialized training in offshore-specific techniques demonstrates your commitment and preparedness. When employers see you've invested your own time and money into offshore-relevant skills, they're more likely to take a chance on you.
When you land that interview, preparation is key. Offshore welding interviews assess both technical skills and cultural fit – after all, you'll be living with these people in close quarters for weeks at a time.
Be ready for questions like: "How would you handle welding in a confined space with poor visibility and limited ventilation?" This isn't just about technical ability – they're assessing your safety awareness and problem-solving skills under pressure.
When they ask, "Describe your experience with welding procedure specifications and how you ensure compliance," they're testing your understanding of documentation and quality requirements – critical in an environment where weld failures can have catastrophic consequences.
Don't be surprised by questions about maintaining welding skills during off-rotation periods. Employers want to know you stay sharp during your time off. Similarly, questions about handling safety violations by senior team members evaluate whether you'll prioritize safety over hierarchy – essential in the offshore world.
Almost every interview includes some variation of: "How flexible are you with rotation schedules and emergency call-outs?" Offshore operations require adaptability when conditions change, and they need to know you can roll with the punches.
"During my interview, they were less concerned with my welding certificates—which they'd already verified—and more focused on whether I'd be a reliable team member in challenging situations," recalls Sarah, recently hired for an offshore wind farm project. "They wanted to know I wouldn't crack under pressure or create conflicts in tight living quarters."
If you're coming from military service, especially with welding experience, you've got a significant advantage in the offshore job market. The discipline and structure of military life mirrors the regimented offshore environment perfectly. Your ingrained safety consciousness and adaptability to challenging conditions transfer beautifully to offshore work.
Military technical training often provides a solid foundation that can be leveraged for civilian qualifications. And that physical fitness you maintained in service? It's exactly what you need for the demanding nature of offshore welding.
Veterans can tap into several resources for this transition, including GI Bill benefits for additional certifications, veteran-focused hiring initiatives by major offshore employers, and specialized placement services. Networking with veterans already working offshore can provide invaluable insights and potential referrals.
"As a Navy veteran who worked on ship repairs, I found the transition to offshore welding natural," explains Robert, former military welder now working in the Gulf of Mexico. "The attention to detail, respect for procedure, and ability to work long hours in confined spaces were skills I'd already developed in service. Companies recognized that value immediately."
At Tentacle Tools, we proudly support veteran welders transitioning to civilian careers, recognizing the exceptional skills and work ethic they bring to the trades. We understand that those who've served our country bring unique qualities to the welding profession – qualities that make for outstanding off shore welders.
Whether you're a veteran or civilian welder looking to break into offshore work, persistence pays off. The path might not be direct, but with the right preparation, certifications, and mindset, you can join the ranks of these specialized tradespeople who keep our offshore infrastructure running safely and efficiently.
Life as an off shore welder means embracing a different rhythm than your typical 9-to-5 job. Instead of weekends off, you'll work intense periods followed by extended breaks.
Most offshore rotations follow predictable patterns – typically 2 to 6 weeks on the platform followed by an equal period at home. The most common schedules are 2-on/2-off, 3-on/3-off, or 4-on/4-off. During your time offshore, expect to work 12-hour shifts, seven days straight, with no days off until your rotation ends.
"The rotation schedule often depends on your experience and the project urgency," explains a veteran welder with 15 years offshore. "When I started, I took whatever schedule they offered. Now, with more experience under my belt, I can usually negotiate my preferred rotation pattern."
Some international or remote locations might require longer hitches – occasionally up to 90 days – though these extended rotations are becoming less common as companies recognize the mental health benefits of more frequent breaks.
The intensity of offshore work is balanced by those weeks of freedom afterward. Many welders use this time to pursue hobbies, spend quality time with family, or even run side businesses. It's a lifestyle that takes adjustment but offers a unique work-life balance once you adapt to its rhythm.
Breaking into offshore welding requires investment in yourself before an employer will invest in you. At minimum, aspiring off shore welders should obtain:
The bare essentials include your BOSIET (Basic Offshore Safety Induction and Emergency Training), which includes that infamous helicopter underwater escape training. This certification is your golden ticket – without it, you simply can't board the helicopter or vessel to reach offshore installations.
You'll also need a current offshore medical certificate proving you're physically fit for the demanding environment. This isn't your standard physical – doctors will thoroughly assess your cardiovascular health, vision, hearing, and overall fitness.
On the technical side, a 6G pipe welding qualification in SMAW (stick welding) is the absolute minimum, though having GTAW (TIG) certification will make you significantly more marketable. Most employers prefer welders coded to multiple processes and materials.
Don't forget your MIST (Minimum Industry Safety Training) certification, which covers essential safety protocols specific to offshore environments.
"I made the mistake of waiting for an employer to fund these certifications," admits one Gulf of Mexico welder. "I wasted a year before realizing I needed to invest in myself first. Once I had the right tickets, I had three job offers within a month."
Additional certifications that will strengthen your application include confined space entry training, fall protection, first aid/CPR, H₂S awareness, and rigging qualifications. Each one makes you more versatile and valuable on a platform where crew size is limited and versatility is prized.
Let's talk about what makes the demanding offshore lifestyle worthwhile for many welders – the paycheck. Experienced off shore welders with 5+ years of offshore time and multiple specialty certifications can earn substantial compensation that makes land-based welding jobs look modest by comparison.
Base salaries typically range from $80,000 to $120,000 annually, but that's just the beginning. Overtime pay – often at time-and-a-half or double-time rates – can significantly boost your earnings, especially during critical projects with tight deadlines.
For underwater welders, depth pay adds another layer of compensation, usually $1-4 additional per foot of depth. This means deep-water jobs can nearly double your daily rate.
"I've seen guys clear $200,000 in good years," shares one North Sea veteran. "It's not typical, but when you combine specialty skills with overtime and project bonuses, the numbers can get pretty impressive."
The highest earners in offshore welding typically combine multiple specialties – like being qualified in both welding and NDT inspection, or welding and rope access. These hybrid specialists can command premium rates because they reduce the total crew size needed.
Regional differences matter too. North Sea operations (particularly Norwegian sectors) and the Gulf of Mexico generally offer higher compensation than some international locations. Tax advantages can also play a role, with some rotational workers benefiting from foreign earned income exclusions depending on their home country's tax laws.
The financial rewards of offshore welding come with trade-offs, but for many welders, the ability to earn in months what might take a year in conventional welding makes the challenging lifestyle worthwhile.
The journey to becoming an off shore welder is demanding but rewarding, offering exceptional compensation, unique experiences, and opportunities for career advancement that few other trades can match. From the specialized training and certifications to the challenging work environments, this career path requires commitment, resilience, and continuous skill development.
For military veterans, the transition to offshore welding feels natural and familiar. The discipline, attention to detail, and ability to work under pressure that you developed in service translate perfectly to life on an oil rig or wind farm. Many veterans find that the structured environment offshore mirrors their military experience, making the adjustment smoother than expected.
"My time in the Navy prepared me for offshore life better than any training program could," shares one veteran-turned-welder. "The long rotations, tight quarters, and emphasis on safety protocols felt like home from day one."
As the offshore energy landscape evolves, welders who stay adaptable will continue to find plenty of opportunities. Traditional oil and gas operations aren't disappearing, but they're now joined by a booming renewable energy sector that needs the same specialized welding skills. Whether you're joining a crew maintaining decades-old platforms or installing cutting-edge wind turbines, your expertise remains in high demand.
The financial rewards make the challenges worthwhile. Six-figure incomes are achievable for experienced professionals, especially those who continue adding specialized certifications throughout their careers. Even better, the rotation lifestyle gives you extended periods at home to enjoy the fruits of your labor – time that many land-based welders simply don't get.
At Tentacle Tools, we're proud to support the skilled trades community not just with American-made specialty welding tools engineered for demanding environments, but also through our dedicated job board connecting welders with opportunities nationwide. We understand the challenges of breaking into specialized fields like offshore welding, and we're committed to equipping tradespeople with both the tools and opportunities they deserve.
Whether you're making your first transition from land-based welding to offshore work, or leveraging your military experience in a new maritime career, the path to becoming an off shore welder offers a challenging yet fulfilling professional journey with rewards that extend far beyond the paycheck.
For more information about welding careers and opportunities, visit Tentacle Tools Careers and explore how our American-made tools are supporting welders in the most demanding environments around the world.
Explore insights, tips, and trends in tech and productivity!