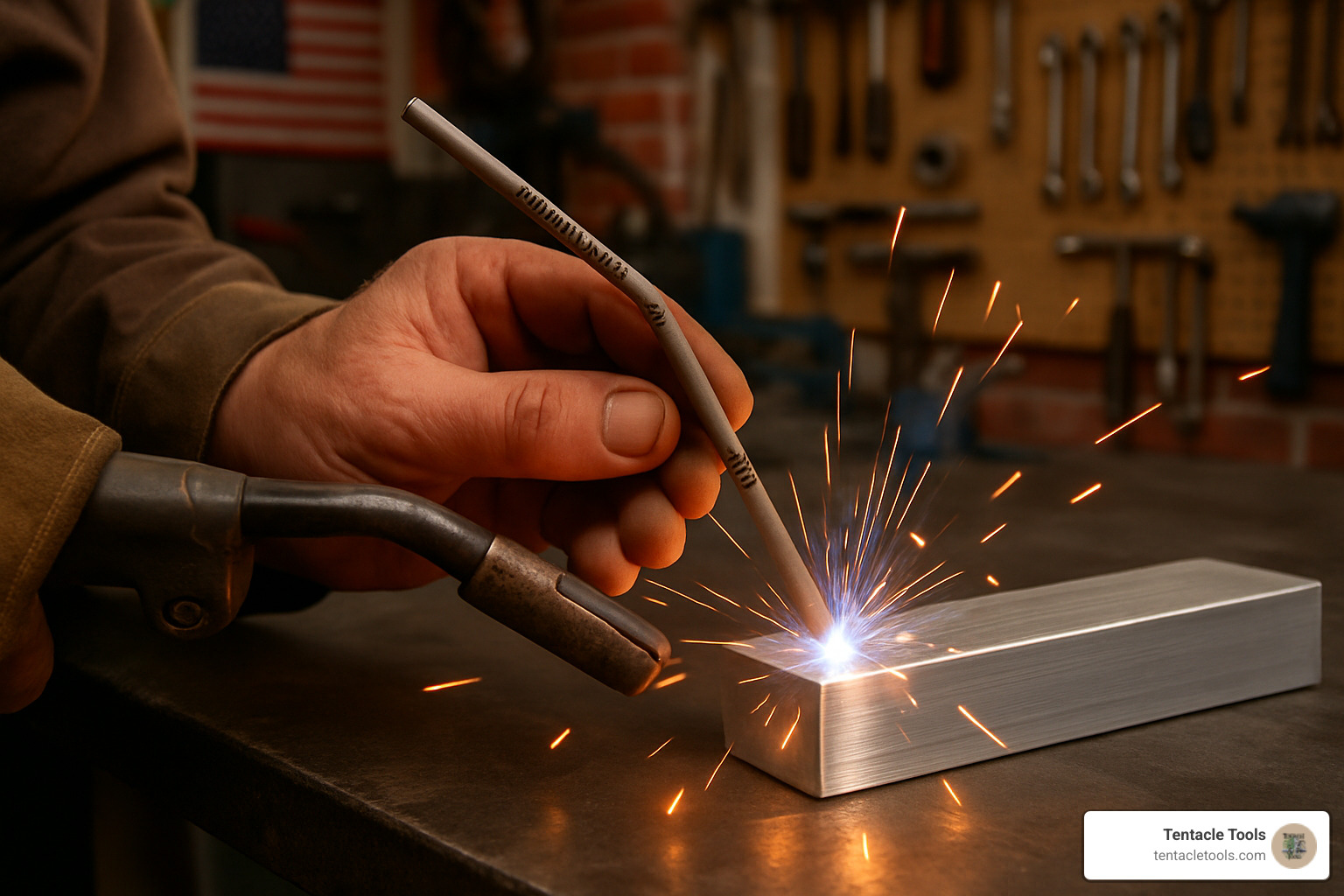
Learn how to e4043 dc aluminum aluminarc specialty welding electrodes for clean, strong aluminum welds. Tips, setup, and troubleshooting inside!
Learning how to e4043 dc aluminum aluminarc specialty welding electrodes work is crucial for any welder tackling aluminum projects. Here's the quick breakdown:
Key Steps for E4043 DC Aluminum Welding:
E4043 DC aluminum "AluminArc" specialty welding electrodes are flux-coated stick electrodes designed specifically for welding aluminum alloys. These electrodes contain 4.5-6% silicon, which gives them excellent fluidity and makes them perfect for welding cast, wrought, and extruded aluminum in all positions.
The big advantage? E4043 electrodes produce welds with approximately 34,000 psi tensile strength and can handle both arc welding and torch brazing applications. They're commonly used for truck beds, loading ramps, engine blocks, and irrigation piping.
Unlike TIG or MIG welding, stick welding aluminum with E4043 electrodes doesn't require shielding gas - the flux coating does all the work. This makes them ideal for outdoor repairs and field work where wind would blow away your gas coverage.
I'm William "Stick" Mank, a second-generation welder with over 20 years in the oil and gas industry, and I've used E4043 electrodes extensively for aluminum repairs in harsh field conditions. Through my experience building specialty tools at Tentacle Tools, I've learned that mastering how to e4043 dc aluminum aluminarc specialty welding electrodes perform can make the difference between a solid repair and a callback.
Basic how to e4043 dc aluminum aluminarc specialty welding electrodes terms:
When you're learning how to e4043 dc aluminum aluminarc specialty welding electrodes work, understanding the fundamentals makes all the difference. These electrodes are the real workhorses of aluminum stick welding, and for good reason.
E4043 DC aluminum "AluminArc" specialty welding electrodes meet AWS A5.3 E4043 specifications and pack a secret weapon: 4.5-6.0% silicon content. That silicon is what gives these electrodes their incredible fluidity and wetting action on aluminum surfaces.
The typical weld deposits you'll get have around 34,000 psi tensile strength with 10-18% elongation. What really sets E4043 apart is its versatility - these electrodes work as all-position rods and can pull double duty for both arc welding and torch brazing applications.
I've seen these electrodes used extensively across multiple industries. Transportation fabrication relies heavily on them for truck beds and loading ramps. Marine applications like docks and banisters benefit from their corrosion resistance. Infrastructure projects use them for stairs and diamond plate work. Agriculture depends on them for irrigation piping repairs, and automotive shops reach for them when dealing with engine blocks and transmission housings.
An E4043 electrode is essentially a flux-coated aluminum stick electrode designed specifically for DC reverse polarity welding. The "E" tells you it's an electrode, and "4043" refers to the aluminum-silicon alloy composition that matches ER4043 filler wire you might use in TIG or MIG welding.
The flux coating creates a stable arc that's easy to control, removes oxides as you weld, protects the molten puddle from contamination, and forms a slag that chips off cleanly when you're done.
When you strike an arc with E4043, you get a smooth, low-spatter arc that produces dense, machinable deposits. The welds match the base aluminum color well and provide excellent corrosion resistance.
E4043 electrodes really shine in specific situations where other welding processes might struggle.
Transportation fabrication is ideal for truck beds, loading ramps, and trailer components. E4043's strength and corrosion resistance make it perfect, and it works in all positions so you can make repairs without tearing apart equipment.
Irrigation piping is another sweet spot. Agricultural systems often need field repairs in windy conditions where shielding gas would blow away. E4043 doesn't need gas coverage.
Maintenance and repair work on cast aluminum is where E4043 really proves its worth. Engine blocks, transmission cases, and other castings often develop cracks that need filling. The electrode's fluidity helps it flow into tight cracks and defects.
For liftd temperature service applications, E4043 welds can handle sustained temperatures above 150°F without problems, making them perfect for components near heat sources.
Getting your workspace ready is where most welders either set themselves up for success or create headaches that last all day. When you're learning how to e4043 dc aluminum aluminarc specialty welding electrodes, the prep work isn't optional - it's what separates clean, strong welds from frustrating do-overs.
Aluminum's invisible oxide layer forms instantly when aluminum touches air. This oxide layer melts at 3,700°F while your base aluminum melts at just 1,220°F. You're trying to weld through a barrier that's nearly twice as heat-resistant as your actual material.
The solution is thorough surface preparation using stainless steel brushes dedicated only to aluminum work. Never use the same brush on steel and aluminum. Cross-contamination will give you porosity and weak welds every single time.
For thicker sections, preheating up to 600°F maximum makes a world of difference. This helps with penetration and reduces thermal shock cracking.
Your machine setup needs DC reverse polarity (DCEP) - electrode positive. This polarity gives you the cathodic cleaning action that breaks up stubborn oxides while you weld. The short-arc technique works best, keeping your arc length to just 1-2 times the electrode diameter.
Amperage settings by electrode diameter run from 50-165 amps depending on size. Start with 3/32" electrodes at 50-85 amps for thinner material, move up to 1/8" electrodes at 75-130 amps for general work, and use 5/32" electrodes at 100-165 amps for heavier sections.
Cleaning aluminum properly isn't complicated, but it has to be done right every time.
Start with degreasing using acetone - this removes oils, fingerprints, and contamination that'll cause problems later. Even oils from your skin can create porosity.
Use dedicated stainless steel abrasives for mechanical cleaning. Work in one direction and clean at least an inch beyond your weld area on each side. The goal is removing that oxide layer completely.
Fit-up and gap control becomes critical with aluminum because of its high thermal expansion. For butt joints, plan on 1/16" gaps for material up to 1/4" thick. Tack weld frequently to prevent distortion.
You need to weld within 30 minutes of cleaning. Aluminum oxide reforms fast, especially when it's humid. Clean it, fit it up, and weld it.
E4043 electrodes are like sponges when it comes to moisture - they'll soak up humidity from the air and cause nothing but trouble. Wet electrodes give you porosity, excessive spatter, and an arc that won't behave.
Keep electrodes in sealed tubes when you're not using them. If you're working in a humid environment, invest in a 250°F rod oven.
Avoid moisture pickup by never leaving electrodes exposed to rain or high humidity. For field work, heated quivers or portable rod ovens are worth their weight in gold.
If your electrodes get damp, you can usually save them by baking at 250°F for a couple hours. Don't go higher or you'll damage the flux coating.
Now we get to the fun part - actually striking that arc and laying down some aluminum! Learning how to e4043 dc aluminum aluminarc specialty welding electrodes work takes practice, but once you get the hang of it, you'll wonder why you ever struggled with aluminum welding.
The biggest difference from steel welding is that aluminum conducts heat about three times faster than steel. This means you need to crank up your amperage and keep moving at a steady pace. The good news is that E4043's silicon content makes the puddle flow like butter when you get it right.
Your electrode angle is crucial here. Hold it at 10-15 degrees from vertical, pushing in the direction of travel. This isn't like steel welding where you can drag the electrode - aluminum welding wants you to push that puddle forward.
Watch that puddle carefully. When everything's dialed in correctly, you'll see a bright, fluid puddle that wets out nicely on both sides of the joint. If it looks dull or isn't flowing well, you probably need more heat or better cleaning.
Getting your machine set up right is half the battle when mastering how to e4043 dc aluminum aluminarc specialty welding electrodes.
First things first - polarity must be DC reverse (DCEP) with the electrode positive. This isn't negotiable with aluminum stick welding. The positive electrode creates the cleaning action that blasts through aluminum oxides.
For electrode diameters: 3/32-inch electrodes run best between 50-85 amps, 1/8-inch needs 75-130 amps, and 5/32-inch wants 100-165 amps. Start on the lower end and work your way up based on how the puddle behaves.
Arc length should be 1-2 times your electrode diameter - no more, no less. Too long and you'll get spatter and porosity. Too short and you'll be stubbing the electrode into the work.
Here's where the rubber meets the road with how to e4043 dc aluminum aluminarc specialty welding electrodes.
Starting your arc requires a scratching motion - like striking a giant match. Once you get it lit, quickly pull back to establish your arc length. Don't tap-start like you might with steel electrodes.
The puddle tells you everything you need to know. E4043's high silicon content makes it flow beautifully when conditions are right. You'll see a bright, almost mirror-like puddle that spreads evenly.
For travel technique, think steady and deliberate. Stringer beads work best on thinner material - just keep moving at a consistent speed. On thicker sections, you can use a slight weave, but keep it narrow.
Multi-pass welding is your friend on thick aluminum. Don't try to fill everything in one pass. Build it up gradually, letting each pass cool just enough to solidify before adding the next layer.
Always fill your craters. Aluminum loves to crack at the end of welds, so take that extra second to properly fill and taper your crater.
E4043 electrodes work in all positions except vertical down. Each position has its own personality, but once you understand the basics, you can make quality welds anywhere.
Flat position is where you want to learn the basics. The puddle behaves predictably, and you can focus on getting your travel speed and heat input dialed in.
Horizontal welding adds gravity to the equation. Angle your electrode slightly upward and pick up your travel speed a bit to keep that fluid puddle from sagging.
Vertical up separates the rookies from the experienced hands. Drop your amperage by 10-15% and keep that puddle small and manageable. Build up in small steps.
Overhead position tests your skills. Lower amperage settings and a tight arc length are your friends here. The flux coating actually helps support the puddle against gravity.
Joint types all respond well to E4043, but each has its tricks. Butt joints need proper fit-up and gap control. Fillet welds require good toe fusion on both legs. Lap joints can be tricky because you need penetration through the overlap without burning through the bottom piece.
Even seasoned welders run into hiccups when mastering how to e4043 dc aluminum aluminarc specialty welding electrodes. Most problems have straightforward fixes once you know what to look for.
Porosity is the biggest headache you'll face with aluminum stick welding. The usual suspects include contaminated base metal that wasn't cleaned thoroughly, wet electrodes that picked up moisture, excessive arc length that breaks down shielding action, or contaminated filler rod.
Lack of fusion shows up as incomplete bonding between weld metal and base material. This typically happens when you're running insufficient amperage, didn't remove all oxides during cleaning, set wrong polarity, or tried welding cold base metal that needed preheating.
Cracking control requires respecting aluminum's thermal characteristics. You need proper joint design with adequate gaps, controlled heat input, preheating consideration for thick sections, and complete crater filling.
Worm tracks look like squiggly porosity patterns that snake through your weld. These indicate hydrogen contamination. Use dry electrodes from proper storage, clean your base metal more thoroughly, and reduce arc length for better atmospheric protection.
Excessive oxides show up as dark, sooty deposits on the weld surface. This means you're not getting proper cathodic cleaning action. Double-check your polarity setting (must be DCEP), and shorten that arc length.
Excessive spatter wastes electrode material. The culprits are usually wet electrodes, excessive arc length, or wrong polarity settings. Keep electrodes bone dry, maintain proper arc length, and verify DCEP polarity.
Cold lap occurs when weld metal sits on top of base metal without actually fusing together. Bump up your amperage settings, improve your base metal cleaning technique, or add preheat for thick sections.
Picking the right aluminum filler alloy can make the difference between a weld that lasts decades and one that fails in the field.
E4043 delivers about 34,000 psi tensile strength and works beautifully with 6XXX series alloys, castings, and applications that see liftd temperatures. The silicon content gives excellent fluidity, and it has low crack sensitivity with heat-treatable alloys. After anodizing, expect a gray color.
ER5356 brings higher strength at roughly 42,000 psi, making it the go-to choice for 5XXX series alloys and marine applications where corrosion resistance is critical. The magnesium content provides extra strength, though it's not quite as fluid as 4043.
ER4047 sacrifices some strength (around 28,000 psi) for maximum fluidity thanks to its high silicon content. This makes it perfect for brazing applications and repair welding where you need the filler to flow into cracks and defects.
For most everyday aluminum welding projects, E4043 hits the sweet spot with its balanced combination of strength, fluidity, and crack resistance. Choose 5356 when maximum strength is non-negotiable and you're working with 5XXX series alloys. Reserve 4047 primarily for brazing operations or repair work where maximum fluidity helps the filler flow into damaged areas.
Working with how to e4043 dc aluminum aluminarc specialty welding electrodes requires serious attention to safety. After twenty years in the oil and gas industry, I've learned that aluminum welding has its own set of hazards that can catch even experienced welders off guard.
The biggest danger is aluminum's deceptive nature - it conducts electricity extremely well and stays dangerously hot long after welding without showing any color change like steel does. The metal looks exactly the same whether it's 70°F or 500°F.
PPE requirements are non-negotiable when aluminum welding. You need a face shield with proper shade settings (typically 10-13 for aluminum), heavy leather gloves, and complete skin coverage. The UV radiation from aluminum welding is particularly intense and can cause severe burns to exposed skin.
Fume extraction is critical because aluminum welding produces different fumes than steel welding. These fumes can be harmful with prolonged exposure, so work in well-ventilated areas or use local exhaust ventilation.
Electric shock prevention takes on extra importance with aluminum because it's such an excellent conductor. Always ensure your workpiece is properly grounded and keep your work area completely dry. Wet conditions and aluminum welding don't mix.
UV arc ray protection goes beyond just wearing a helmet. Aluminum welding produces intense UV radiation that can cause severe skin burns and eye damage. Make sure anyone working nearby has proper protection or use welding screens to contain the arc flash.
Hot surface handling requires special attention because aluminum gives no visual cues about temperature. We always mark hot workpieces with chalk or use signs, and we never rush the cooling process. Keep a fire extinguisher nearby.
Ventilation requirements are more critical with aluminum than many other metals. The welding process generates ozone from UV radiation, plus aluminum-specific fumes that need proper extraction.
Stress-relief cool-down is crucial for aluminum welds because of the metal's high thermal expansion rate. Let thick sections cool gradually to prevent thermal stress cracking. Never quench aluminum welds in water - the rapid cooling can cause immediate cracking.
Post-weld wire brushing should only be done with stainless steel brushes dedicated to aluminum work. The flux residue from E4043 electrodes comes off easily, but cross-contamination from steel brushes can cause corrosion problems down the road.
Anodizing considerations are important if your project will be anodized later. E4043 welds typically produce a gray color when anodized, which may not perfectly match the base aluminum.
The key to successful post-weld care is patience. Aluminum doesn't forgive rushed work, and proper cooling and cleaning take time. But when done right, E4043 welds provide excellent corrosion resistance and long service life.
After years of teaching welders how to e4043 dc aluminum aluminarc specialty welding electrodes work, I get the same questions over and over. Here are the three most common ones that can make or break your aluminum welding success.
When you're welding 6061 aluminum base metal with E4043 electrodes, you can expect approximately 34,000 psi tensile strength with 10-18% elongation. The yield strength typically runs around 19,000-20,000 psi. These numbers are solid for most structural applications, though they're not as high as what you'd get with 5356 filler alloy.
What really matters is that E4043 welds are dense and porosity-free when you use proper technique. They're also machinable, which is huge if you need to do any post-weld machining work. The welds provide excellent corrosion resistance and give you a good color match with the base aluminum.
Here's something critical to remember: these properties are for as-welded conditions only. Unlike steel, you can't heat treat aluminum welds after welding to bump up the strength. What you weld is what you get, so getting your technique right the first time is essential.
This is one of the coolest features of E4043 electrodes - they're dual-purpose tools. You can absolutely use them for both arc welding and torch brazing applications. For torch brazing, you'll need to grind off the flux coating first, then use the bare rod with an oxy-acetylene torch and proper aluminum brazing flux.
This versatility makes E4043 electrodes incredibly valuable for repair work where you might need both welding and brazing techniques on the same job. The silicon content that makes them flow so well during welding also provides the fluidity you need for effective brazing.
Torch brazing with E4043 works great for joining dissimilar metals, repair welding where you don't need full penetration, and situations where the lower heat input of brazing helps prevent distortion. I've used this technique countless times for delicate cast aluminum repairs where full welding heat would cause cracking.
Porosity in cast aluminum is the bane of every welder's existence, but it's totally manageable once you understand the causes. The culprits are usually surface contamination, gas entrapment in the casting, and moisture.
Start with aggressive surface preparation. Cast aluminum often has oil, paint, or other nasty stuff on it. Clean everything with solvent first, then follow up with mechanical cleaning using stainless steel brushes. Pay extra attention to machined surfaces where cutting fluids love to hide.
Preheating is your secret weapon for cast aluminum. Heat the casting to 400-600°F to drive out moisture and improve wetting action. This is especially important for old castings that have been sitting around absorbing moisture for years.
For your welding technique, use a shorter arc length and slightly higher amperage to get good cleaning action. Make multiple passes instead of trying to fill large areas in one shot. And always make sure your electrodes are bone dry - wet electrodes will give you porosity every single time.
If you're still getting porosity after all this, the casting itself might have internal porosity that's getting exposed during welding. In really bad cases, you'll need to grind out the porous areas and build them back up with multiple passes. It's more work, but it's the only way to get a sound weld.
Learning how to e4043 dc aluminum aluminarc specialty welding electrodes work isn't just about mastering another welding technique - it's about expanding your capabilities as a tradesman and opening doors to better opportunities. These electrodes have saved my bacon more times than I can count during field repairs where TIG or MIG welding just wasn't practical.
What makes E4043 electrodes special is their versatility. DC reverse polarity setup, thorough aluminum cleaning with dedicated stainless steel brushes, proper electrode storage, and short arc length control - master these fundamentals and you'll be welding aluminum like a pro. The fact that they work without shielding gas makes them invaluable for outdoor work where wind would blow away your gas coverage.
At Tentacle Tools, we understand what it's like to be out in the field when something breaks down and needs fixing yesterday. That's why we're committed to more than just manufacturing specialty welding tools - we're about building up the entire skilled trades community. Our American-made products are designed by welders who've been in your boots, facing the same challenges you face every day.
The backbone of America runs on skilled trades. Whether you're working pipeline, oil and gas, or fabrication, aluminum welding skills make you more valuable and more employable. We've seen welders double their earning potential just by adding aluminum capabilities to their skill set.
We're not just selling tools - we're building careers. Check out our job board where we connect skilled welders with opportunities across the country. And when you're ready to upgrade your tool arsenal, browse our catalog for specialty welding tools engineered by tradesmen who understand what really matters on the job.
Every journey starts with a single step, and every expert was once a beginner who decided to keep learning. The trades built this great nation, and they'll continue driving our economy forward with professionals who take pride in their craft. Stay safe out there, keep practicing, and never stop pushing yourself to be better.
That's the Tentacle Tools way - American grit, quality tools, and the determination to help every welder succeed.
Explore insights, tips, and trends in tech and productivity!