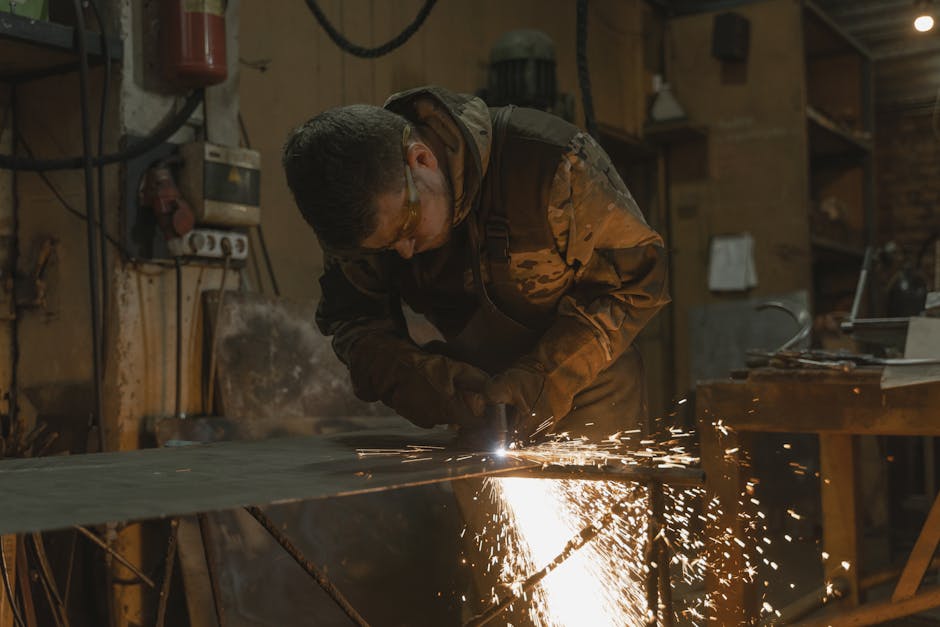
Discover how to become a specialty welder with expert tips on skills, certifications, salaries, and top career paths. Start your journey!
How to become a specialty welder requires specific training, certifications, and hands-on experience beyond general welding skills. If you're looking for a quick answer, here's the essential pathway:
Step | Requirement | Timeline |
---|---|---|
1 | High school diploma or GED | Prerequisite |
2 | Complete basic welding training | 6-12 months |
3 | Gain general welding experience | 1-2 years |
4 | Pursue specialty-specific training | 3-12 months |
5 | Obtain specialty certifications (AWS, ASME, API) | 2-4 months |
6 | Complete apprenticeship or OJT | 1-4 years |
7 | Maintain certifications & continue education | Ongoing |
Specialty welding isn't just a job—it's a career path that can take you from shipyards to aerospace facilities, from underwater pipelines to nuclear power plants. While general welders join metal using standard techniques, specialty welders master complex processes for critical applications where failure isn't an option.
The American Welding Society reports that skilled specialty welders are in high demand, with the Bureau of Labor Statistics showing that the best-paid welders earn more than $63,660 annually. Texas leads employment with over 45,000 estimated annual welding job openings nationwide.
Why consider specialty welding? Beyond better pay, you'll gain:
As one underwater welder put it, "This isn't just welding—it's welding while fighting the elements. The challenges make the victories that much sweeter."
At Tentacle Tools, we've equipped specialty welders for decades and seen how this career path rewards those willing to put in the work and continuously develop their skills.
In this comprehensive guide, we'll walk you through everything you need to know about becoming a specialty welder:
Think of general welding as driving a car on city streets, while specialty welding is more like racing Formula 1 on a wet track. Both involve similar basic skills, but the stakes, precision, and expertise required are worlds apart.
"The difference between general and specialty welding is like comparing a house painter to a fine art restorer," explains James Harmon, a 20-year veteran pipe welder who now trains apprentices. "Both are skilled, but specialty welders work with tighter tolerances, exotic materials, and under conditions where failure could mean catastrophic consequences."
When you're joining critical components in a nuclear facility or welding underwater on an oil rig, there's zero room for error. Specialty welders don't just join metal—they create connections that must withstand extreme pressures, temperatures, and stresses while meeting strict industry codes.
What truly sets specialty welding apart is the materials involved. While general welders typically work with mild steel, specialty welders master exotic alloys like Inconel, titanium, and chrome-moly. These materials don't forgive mistakes and demand perfect heat control and technique.
The inspection process is another major difference. A general weld might just need a visual check, but your specialty welds will likely face the "truth machine"—X-ray testing that reveals even the tiniest flaws invisible to the naked eye. Many specialty welds undergo ultrasonic or dye penetrant testing too, because when you're welding components for aerospace or pressure vessels, hidden defects can lead to disaster.
Code compliance becomes your daily language in specialty welding. You'll need to know ASME, API, or AWS D1.1 standards like the back of your hand. And unlike general welders, you'll need to recertify every six months through testing or documented quality work—a requirement that keeps standards high and pretenders out of the field.
The working environments also separate the specialists from the generalists. From underwater depths to clean rooms, confined spaces to dizzying heights, specialty welders adapt their skills to conditions that would make most folks think twice.
Not everyone is cut out for the demands of specialty welding. Beyond basic welding ability, you'll need a specific set of skills and traits to thrive.
Exceptional hand-eye coordination is non-negotiable when you're making precision welds in awkward positions or with limited visibility. Your hands need to be steady as a surgeon's, especially when working with thin materials where the margin for error is measured in thousandths of an inch.
Physical stamina becomes crucial when you're contorted into uncomfortable positions for hours. Whether you're welding pipe in a trench or working inside a pressure vessel, specialty welding often means holding awkward positions that test your endurance.
You'll also need solid math skills to calculate dimensions, angles, and heat inputs with accuracy. "I use more trigonometry as a pipe welder than I ever thought I would in high school," jokes veteran welder Mike Ramos.
Blueprint reading is essential—you'll need to interpret complex technical drawings and translate them into perfect welds that meet exact specifications. Those blueprints aren't suggestions; they're requirements that must be followed to the letter.
When things go sideways—and they will—your problem-solving abilities will be tested. Maybe your workspace is too confined for standard equipment, or environmental conditions are affecting your arc stability. Specialty welders think on their feet and adapt.
"I've trained hundreds of welders," says certification instructor Maria Delgado, "and the ones who excel in specialty fields are those who treat every weld like it's going to be X-rayed—because it probably will be." This speaks to the attention to detail that separates good welders from great ones.
Most specialty welding happens in teams, so communication skills matter. You'll coordinate with engineers, inspectors, pipefitters, and other trades to ensure everything comes together perfectly.
Finally, an unwavering commitment to safety is essential. When you're welding in confined spaces, at extreme depths, or around hazardous materials, one mistake can have serious consequences. At Tentacle Tools, we've seen that the best specialty welders are those who never compromise on safety, no matter the deadline pressure.
The world of specialty welding isn't just a job – it's a universe of diverse career paths where your skills can take you from ocean depths to the frontiers of aerospace. Each specialty offers its own unique blend of challenges, rewards, and opportunities for growth.
Underwater Welding isn't for the faint of heart. Imagine combining the precision of welding with the challenges of commercial diving – limited visibility, bone-chilling temperatures, and the constant pressure of the deep. It's why these professionals earn between $100,000-$300,000+ annually. As Navy veteran and underwater welder Jake Martinez puts it, "Every day brings a new challenge – one day you're repairing an oil platform in the Gulf, the next you're working on a dam in near-zero visibility." The trade-off for those impressive paychecks? A fatality rate 40 times higher than the national average for all occupations.
Pipeline Welding offers the freedom of the open road combined with serious earning potential. These modern-day nomads follow the pipeline projects across America, often living out of their trucks with their welding rigs in tow. With API 1104 certification and mastery of the challenging 6G position, top pipeline welders can pull in over $7,000 weekly on critical projects. The work is tough – battling weather extremes, remote locations, and the pressure of knowing your welds will transport volatile materials for decades – but for many, the independence and pay ($50,000-$185,000+ annually) make it worthwhile.
Nuclear Welding demands perfection where there's zero room for error. Working in power plants means dealing with radiation exposure, confined spaces, and documentation requirements that would make a lawyer sweat. "It's not just about making beautiful welds," explains 15-year nuclear welding veteran Sarah Johnson. "It's about proving everything you do meets the highest standards mankind has ever created for metal joining." The reward for this precision? Stable employment and salaries ranging from $65,000-$120,000+ annually.
Aerospace Welding is where precision meets innovation. When you're joining components for aircraft and spacecraft, tolerances are measured in thousandths of an inch, and materials like titanium and Inconel demand perfect technique. AWS D17.1 certification opens doors to clean room environments where your welds might one day orbit Earth or travel to Mars. The industry pays well ($55,000-$95,000+ annually) for good reason – some aerospace welds undergo testing that costs more than the parts themselves.
Robotic Welding Programming bridges the gap between traditional craftsmanship and cutting-edge technology. As manufacturing evolves, those who can both weld and program the robots that weld are becoming increasingly valuable. "I still use everything I learned as a hands-on welder," says robotic systems specialist Marcus Lee. "But now I'm teaching the robots to do what my hands used to do." This growing field offers comfortable working conditions and salaries ranging from $60,000-$100,000+, with the AWS now offering a Certified Robotic Arc Welding credential.
Automotive Manufacturing welders are the backbone of vehicle production, creating the structures that keep drivers safe in collisions. From resistance spot welding to aluminum MIG work, these specialists work in high-volume environments where speed and consistency are paramount. Did you know a modern car contains over 5,000 spot welds? As vehicles evolve toward lighter materials for fuel efficiency, welders with advanced skills can earn $45,000-$80,000+ while enjoying the stability of major manufacturers.
Artistic Metalwork transforms welding from industrial process to creative expression. These welders-turned-artists create everything from delicate garden sculptures to massive public installations, architectural elements, and custom furniture. Income varies wildly ($40,000+ to six figures for established artists), but the reward comes in seeing your creations become permanent fixtures in homes, businesses, and public spaces. "I still use the same basic welding principles I learned in trade school," notes metal artist Carmen Valdez, "but now I'm creating pieces that move people emotionally, not just structurally."
Historic Restoration specialists are part welder, part historian. They're called upon to repair century-old ironwork, recreate architectural elements from historic photographs, and ensure that restorations honor original craftsmanship while meeting modern safety standards. This specialty ($45,000-$75,000+ annually) attracts those fascinated by traditional metalworking techniques and the satisfaction of preserving America's architectural heritage for future generations.
At Tentacle Tools, we've equipped specialty welders across all these fields with American-made tools designed by people who understand the daily challenges of the trade. Whether you're considering your first specialty welding career or looking to transition between specialties, understanding these diverse paths is the first step in your journey to becoming a specialty welder who stands out from the crowd.
Ready to turn your welding passion into a specialized career? Let's map out your journey to becoming a specialty welder with actionable steps that have helped thousands of tradespeople level up their careers and earning potential.
While you might be eager to fire up a torch, don't skip this foundation. Nearly all specialty training programs require at least a high school diploma or equivalent.
Focus on math classes like algebra and geometry—you'll use these daily when calculating angles and dimensions for precision work. Shop classes give you that early hands-on experience that's invaluable. Don't overlook science courses either; understanding the chemistry of metals and physics of heat transfer will make you a smarter welder. And those English classes? They matter when you're communicating with engineers or writing up inspection reports.
"I see it all the time," says Darrell Williams, who trains welders for pipeline work. "Guys with natural talent hit a ceiling because they struggle with the math needed for advanced certifications. Don't let that be you."
Before diving in, take time to find your perfect fit in the welding world. Ask yourself some honest questions: Do you thrive outdoors or prefer climate-controlled shops? Are heights your thing, or would you rather work at ground level? How much travel can your lifestyle handle?
The Bureau of Labor Statistics shows steady demand for skilled welders through 2031, with hotspots in Texas, California, and Pennsylvania. Research your local market—sometimes the best opportunities are in your backyard.
Training options vary widely, from community colleges and technical schools to union apprenticeships and military programs. Costs range from a few thousand dollars to over $20,000, but don't let that scare you off. The AWS Foundation awards over $2 million in scholarships annually to help welders-in-training.
Career counselor Renee Martinez offers practical advice: "Spend a day shadowing professionals in different specialties before committing. What looks exciting in YouTube videos might feel very different when you're doing it eight hours a day in July heat."
Want to explore specialty welding trends? Check out our blog articles for insights from working professionals.
Quality training isn't just nice to have—it's essential for specialty welding success. Look for programs with AWS SENSE accreditation, which ensures curriculum meets industry standards.
Your options typically include:
When evaluating schools, check for instructors with real-world experience in your target specialty. Modern equipment matters too—learning on outdated machines won't prepare you for today's workplaces. Ask about job placement rates and visit facilities if possible.
Mike Rowe, a welding instructor with shipyard experience, emphasizes: "The best programs balance theory with plenty of booth time. Understanding why you're adjusting amperage is just as important as knowing how to do it."
Classroom knowledge is just the beginning—real skill comes through supervised work experience. This is where you transform from student to professional.
Formal apprenticeships typically run 3-5 years, combining paid work with ongoing education. Union programs like those offered by the United Association (UA) provide structured training with progressive wage scales—starting around 50-60% of journeyman rates and increasing as you master new skills.
Many employers also offer on-the-job training, hiring entry-level welders and developing them into specialists. Whatever path you choose, finding a mentor is gold. Having an experienced eye watching your technique and offering feedback accelerates your growth tremendously.
Jason Torres, who now specializes in underwater welding, reflects: "My apprenticeship pushed me harder than my military training ever did. Having seasoned divers critique every move made me twice the welder I would have been learning on my own."
Certifications aren't just paperwork—they're your passport to better opportunities and pay. Each specialty has its own requirements:
AWS Certified Welder (CW) serves as the foundation for many specialties. ASME Section IX opens doors in pressure vessel and power generation work. API 1104 is the gold standard for pipeline welders. For structural steel, you'll need AWS D1.1 certification.
The process typically involves studying the relevant code, practicing the required procedures, then performing test welds at an Accredited Testing Facility. Your welds will undergo rigorous inspection—visual checks, X-rays, bend tests—before you receive certification. And remember, most certifications require renewal every six months.
"A certification isn't just a piece of paper," AWS instructor Carlos Mendez often tells his students. "It's proof that your work meets national and international standards of excellence. Employers pay for that assurance."
For the latest research on welder demand and certification requirements, check the Bureau of Labor Statistics occupational outlook.
In specialty welding, your work speaks volumes. Document your achievements with photos of completed projects (where security protocols allow). Save those perfect X-ray reports showing defect-free welds. Collect recommendation letters from supervisors and inspectors who've witnessed your quality work.
Establish a professional online presence through LinkedIn, showcasing your certifications and experience. Join industry groups and attend trade shows—the connections you make can lead to opportunities that never hit job boards.
Pipeline supervisor Sarah Johnson puts it plainly: "The welding community is smaller than you think. Your reputation—good or bad—will follow you from job to job. Quality work and professionalism get remembered."
With training complete and certifications in hand, you're ready to launch your specialty career. Be prepared to start in adjacent roles—helper, fitter, or general welder—to get your foot in the door. Most employers will require you to pass a practical welding test before hiring, regardless of your certifications.
The learning journey never ends in specialty welding. Technologies evolve, new alloys emerge, and techniques improve. Continuing education isn't optional—it's how you stay employable and advance your career. With experience, you might become a lead welder, supervisor, inspector, or even start your own specialty business.
"I'm still taking classes and earning new certifications after 12 years," shares aerospace welder Tom Nguyen, who started as a general fabricator. "In this field, standing still means falling behind."
How to become a specialty welder is a journey of continuous improvement, but the rewards—financial security, professional respect, and the satisfaction of mastering a challenging craft—make every step worthwhile.
For job opportunities specifically in specialty welding, check out the Tentacle Tools careers board, where we connect skilled tradespeople with employers who value quality craftsmanship.
Behind every successful specialty welder stands a foundation of proper certifications, a commitment to safety, and a clear understanding of earning potential. This trio forms the backbone of a sustainable, rewarding career in the field.
Walking into a specialty welding position without proper credentials is like showing up to a gunfight with a butter knife – you're simply not equipped for success.
For underwater welders, the journey begins with Commercial Diving certification, followed by the AWS D3.6M Underwater Welding Code certification. You'll also need Hyperbaric Chamber Operations training – because understanding decompression isn't optional when you're working at depth.
Pipeline welders need to secure their API 1104 certification, which has become the gold standard in the industry. The challenging 6G position qualification (welding pipe fixed at a 45° angle) separates the professionals from the amateurs. For high-pressure applications, add ASME Section IX to your credentials.
In the aerospace world, precision is everything. The AWS D17.1 Fusion Welding for Aerospace Applications certification opens doors, while NADCAP compliance ensures you can work on components where failure isn't an option. Clean room protocol certification rounds out your qualifications.
Nuclear welders operate in one of the most regulated environments, requiring ASME Section III certification, Nuclear Quality Assurance-1 (NQA-1) training, and Radiation Worker training.
"Certification is your passport in specialty welding," explains AWS certification specialist Maria Gonzalez. "Without it, doors simply won't open, no matter how skilled you are."
The American Welding Society's certification programs provide internationally recognized credentials that often serve as the entry point for specialty careers.
When you're welding in extreme environments, standard safety practices are just the beginning.
Underwater welders face a perfect storm of hazards – drowning risks, decompression sickness, and the ever-present danger of electric shock in a conductive environment. Add limited visibility, challenging communication, and the occasional curious marine life, and you've got a job that demands constant vigilance.
High-pressure pipe welders contend with the threat of explosive decompression, exposure to toxic gases, and often work in remote locations where medical help isn't just around the corner. Extreme weather conditions can add another layer of complexity to an already demanding job.
The seemingly controlled environments of aerospace and nuclear welding bring their own challenges – radiation exposure, exotic metal fumes that standard ventilation might not adequately address, confined space entry, and the psychological pressure of knowing your work will undergo scrutiny that can detect flaws invisible to the naked eye.
"Safety isn't just about following rules—it's about developing a mindset where you constantly evaluate risks," says OSHA consultant and former specialty welder Jack Martinez. "The best specialty welders I know are almost paranoid about safety, and that's why they've had long careers."
At Tentacle Tools, we understand these unique challenges. That's why our catalog of tools includes innovations specifically engineered to address the safety concerns specialty welders face every day.
The most successful specialty welders share one trait – they never stop learning.
Many experienced specialists eventually become Certified Welding Inspectors (CWI), leveraging their field knowledge into inspection roles that can pay $70,000-$100,000+ annually. Others pursue Welding Engineering Technology degrees, opening doors to technical management positions where they can influence how projects are designed and executed.
As materials and processes evolve, staying current with specialized process training in exotic materials or new joining methods becomes essential. And for those with entrepreneurial ambitions, business management education provides the foundation for launching specialty welding companies.
Financial support for this continued growth is available – the AWS Foundation awards over $2 million in scholarships annually. Many employers also offer tuition assistance, recognizing that better-educated welders deliver better results.
"I've seen welders go from the shop floor to the engineering office by continually investing in their education," notes veteran welding educator Dr. James Wilson. "The ceiling is only as low as you allow it to be."
Let's talk about what matters to many considering this career path – the money.
The Bureau of Labor Statistics puts the median annual salary for welders at $48,940 (May 2023), but that figure barely tells the story for specialty welders. Top earners (90th percentile) make $63,660+ annually in standard positions, while specialty premiums can dramatically increase these figures.
Underwater welders can earn $100,000-$300,000 depending on depth and danger, while pipeline welders on remote projects often make $3,000-$7,000 weekly – numbers that can translate to six-figure annual incomes for those willing to put in the hours.
Geography plays a major role in compensation. Alaska leads the pack with average earnings of $69,370, followed by Hawaii ($68,690), Washington ($63,160), Wyoming ($60,620), and North Dakota ($58,260).
Industry concentrations create regional hotspots. The oil and gas sector drives demand along the Gulf Coast, Alaska, and North Dakota. Shipbuilding creates opportunities in Virginia, Maine, and Washington. Aerospace manufacturing clusters in Washington, California, and Texas, while defense work spreads across military installations nationwide.
"Location flexibility can dramatically increase your earning potential," advises career counselor David Chen. "The welders I know who are willing to travel for shutdown work or remote projects often double or triple what their stay-at-home counterparts make."
For those looking to maximize their earning potential, the willingness to go where the work is – whether that's on an offshore platform, a remote pipeline project, or a classified defense installation – can be the difference between a good living and an exceptional income.
When I talk with aspiring welders, timeline and cost questions always come first. The honest answer? It depends on your path and specialty choice.
Most folks need about 2-6 years from their first welding class to becoming a fully qualified specialty welder. The journey typically includes 6-24 months of initial education, followed by 1-4 years of apprenticeship or hands-on experience. Some specialties, like underwater welding, require additional training that can add another year to your journey.
As for costs, prepare for an investment in your future. Certificate programs at technical schools generally run $5,000-$15,000, while associate degrees at community colleges might cost $8,000-$20,000. Don't forget about certification fees ($35-$1,065 per certification) and your personal gear ($1,000-$3,000 for quality tools).
"The sticker shock scared me at first," admits Carlos, a pipeline welder from Texas. "But I used the GI Bill from my military service, and my first year's salary bump more than covered my training costs."
You don't have to shoulder these costs alone. Look into:
Financial aid counselor Patricia Lee puts it perfectly: "Education is an investment, not an expense. When you compare the training costs to the lifetime earning potential of specialty welders, the return on investment is exceptional."
While you might find entry-level welding jobs without a diploma, the path to specialty welding almost always requires at least a high school education or GED.
Here's why it matters: Almost every accredited welding school and formal apprenticeship program requires a diploma or GED for admission. More importantly, specialty welding involves complex calculations that build directly on high school math fundamentals. Without that foundation, you'll struggle with the precision this work demands.
"I dropped out in 11th grade and hit a wall trying to advance," shares Mike, now a successful pipe welder. "I had to pause, get my GED, and then restart my training. It set me back a full year."
Employers hiring for premium specialty positions typically have minimum education standards too. They need to know you have the basic skills to learn complex processes and follow detailed instructions.
If you don't have a diploma or GED yet, make that your first priority. It's the foundation everything else will build upon.
Start with the AWS Certified Welder (CW) credential as your foundation. This widely-recognized certification verifies your fundamental welding skills and opens doors to entry-level positions where you can gain experience.
From there, follow this natural progression:
Pursue position certifications in 3G (vertical), 4G (overhead), and eventually 6G (inclined pipe), which demonstrate your ability to weld in challenging positions.
Add code-specific certifications based on your specialty interest – API 1104 for pipeline work, ASME Section IX for pressure vessels, or AWS D17.1 for aerospace applications.
What makes the AWS CW program particularly beginner-friendly is its accessibility. You don't need prerequisites or mandatory courses – just the ability to perform quality welds. Testing happens at Accredited Testing Facilities (ATF) nationwide, with a base certification fee of just $35 (though testing facilities charge additional fees). Maintaining your certification requires submitting a simple form every six months.
"I recommend getting comfortable with the testing process early," says Robert Johnson, a certification specialist I spoke with. "The AWS CW gives you that recognized credential to build on while you gain experience and figure out which specialty best fits your interests and abilities."
Specialty certifications require renewal – typically every 6 months – so budget for ongoing testing as part of your career maintenance.
The journey to specialty welding isn't just about picking up a torch—it's about forging a career path built on precision, dedication, and continuous improvement. While the road may be demanding, those who commit to mastering this craft find themselves among an elite group of tradespeople whose skills are always in demand.
Hard work pays off. Throughout this guide, we've walked through the steps of how to become a specialty welder, from foundational education to specialized certifications. The path requires investment—in time, education, and personal growth—but the rewards match the effort. Specialty welders enjoy not just competitive compensation, but the deep satisfaction that comes from mastering complex skills few others possess.
Your reputation is built one weld at a time. In this field, your work quite literally speaks for itself. Every clean X-ray, every passed inspection, and every project completed to specification builds not just your skills but your professional standing. As veteran pipe welder Mark Johnson often tells his apprentices, "In specialty welding, there's nowhere to hide poor craftsmanship—and no greater pride than knowing your welds will hold for decades."
At Tentacle Tools, we understand the challenges specialty welders face because we've been there ourselves. Our American-made welding tools are designed by people who've stood in your boots, facing the same challenges you'll encounter on your path. We're proud to create equipment that supports the precision and reliability your work demands.
The learning never stops. Even the most experienced specialty welders continue developing their skills, adapting to new technologies and techniques. Stay connected with the broader welding community through resources like our blog articles and industry events where knowledge sharing happens naturally.
Specialty welding rewards those with grit and a commitment to excellence. The infrastructure that powers our nation—from pipelines to power plants, from aerospace components to artistic architectural elements—depends on the skilled hands and sharp minds of specialty welders.
Whether you're just striking your first arc or looking to specialize after years in general welding, we hope this guide has illuminated your path forward. America needs skilled specialty welders now more than ever, and with the right training, certifications, and mindset, you can build a rewarding career that offers both personal satisfaction and financial stability.
As we like to say at Tentacle Tools: Behind every great infrastructure project stands a specialty welder who refused to settle for "good enough."
Explore insights, tips, and trends in tech and productivity!