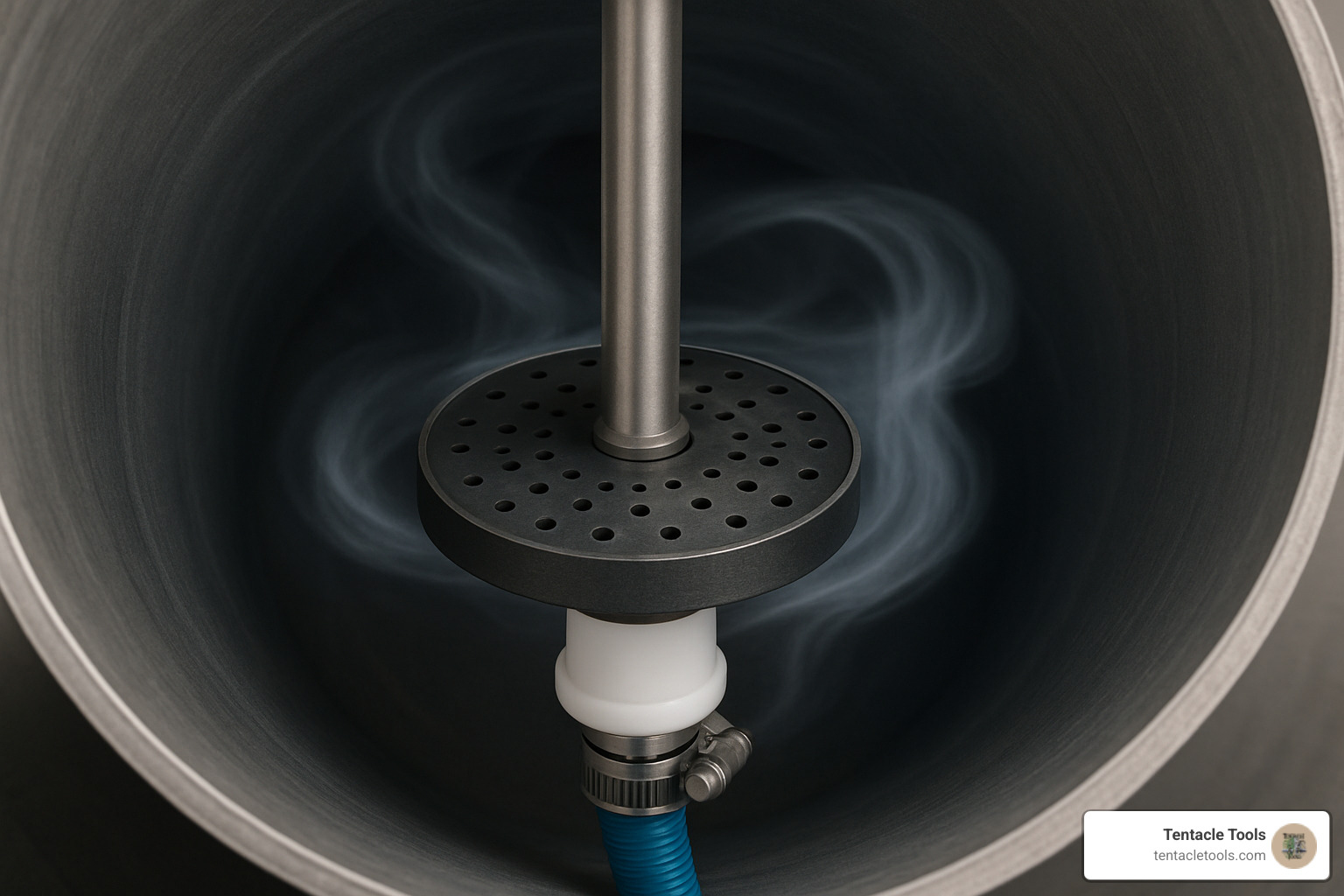
Unlock perfect welds! Understand how an argon purge diffuser eliminates oxygen, saves gas, and boosts quality.
An argon purge diffuser is a specialized tool that creates a uniform, inert atmosphere inside pipes and vessels during welding by evenly distributing argon gas to displace oxygen and other contaminants. This prevents oxidation, "sugaring," and weld defects that can compromise the integrity of critical welds.
Quick Answer for Argon Purge Diffusers:
Picture this: you're welding a critical stainless steel connection, and when you flip that pipe over, the root looks like it's been attacked by rust - heavily oxidized and "sugared." That's what happens when oxygen contaminates your weld zone.
For critical stainless steel welding applications, you need oxygen levels below 100 ppm to achieve that perfect, clean root pass. A simple lighter test won't cut it - that flame needs over 18.8% oxygen to stay lit, which is still way too high for quality welding.
The difference between a properly purged weld and a contaminated one isn't just cosmetic. It's about weld integrity, material properties, and whether your work passes inspection the first time.
I'm William "Stick" Mank, and after 20 years in the oil and gas industry, I've seen too many welders struggle with inconsistent purging that leads to rework and wasted time. That's why I developed argon purge diffuser systems at Tentacle Tools that deliver the uniform gas coverage you need for professional results every time.
Argon purge diffuser vocab to learn:
Think of an argon purge diffuser as your insurance policy against weld contamination. When you're working with stainless steel, titanium, or Inconel, this tool is what separates a professional job from a costly do-over.
Here's the deal: back purging is all about creating a clean, oxygen-free environment inside your pipe before you strike that arc. Without it, atmospheric contaminants like oxygen and moisture sneak into your weld zone and wreak havoc on your root pass.
Ever seen a stainless steel weld that looks like sugar crystals on the back side? That's what we call "sugaring" - and it's a dead giveaway that oxygen contaminated your weld. In Tungsten Inert Gas welding, especially on critical applications, the back side of your weld needs to be just as clean as the face.
When you're welding pipe for pharmaceuticals, food processing, or high-pressure systems, contamination isn't just ugly - it's dangerous. Weld integrity depends on keeping those atmospheric nasties away from your molten metal.
I've watched too many welders try to purge with just a garden hose stuck in one end of a pipe. Gas comes out, but you get turbulent flow, air pockets, and spotty coverage. The result? Weld discoloration, failed inspections, and expensive rework.
The whole point of purging is simple: get the oxygen out and keep it out. Atmospheric contaminants - oxygen, moisture, and nitrogen - are like kryptonite to clean welds. When these troublemakers mix with molten metal, they cause oxidation and mess with your metallurgical properties.
Your root pass is where the magic happens. This first, full penetration weld forms the backbone of your joint. If oxygen contaminates the root, no amount of filler passes will fix the underlying problems.
For pressure vessels, sanitary tubing, and high-purity applications, the back side of your weld has to be spotless. That's where creating an inert weld zone becomes non-negotiable. A proper purging system protects the entire weld area, not just the parts you can see.
Argon isn't just another welding gas - it's the heavyweight champion of purging applications. As an inert gas, argon plays nice with molten metal. It won't react with your specialty alloys or cause unwanted chemical reactions.
Here's the science that matters: argon is heavier than air, so it naturally settles and pushes out lighter atmospheric gases. This density advantage gives you better arc stability and superior heat transfer compared to other options.
When you're welding stainless steel or titanium, argon prevents the chemical reactions that cause discoloration and contamination. For high-purity applications in aerospace, pharmaceutical, and food processing, argon's inert properties are absolutely critical.
After 25 years in the field, I can tell you that argon has proven itself time and again. Unlike other gases that might introduce unwanted reactions, argon keeps your welds clean and your metallurgical properties intact.
Ever watch a welder try to purge a pipe with just a hose shoved in one end? It's like trying to fill a swimming pool with a garden hose pointed at one corner - you'll get there eventually, but it's going to be messy, wasteful, and take forever.
The magic of a quality argon purge diffuser lies in how it transforms chaotic gas flow into something smooth and controlled. When you blast argon through an open hose, you create turbulent flow that actually mixes with the air you're trying to displace. It's counterproductive and wastes your gas.
A proper diffuser changes everything. Through sintered metal construction or carefully designed multiple ports, it breaks down that rushing gas into gentle, uniform streams. This creates what we call laminar flow - smooth, controlled gas movement that systematically pushes out contaminated air without creating the turbulence that causes problems.
The real game-changer is 360-degree coverage. Air pockets are the enemy of clean welds, and they love to hide in the top of pipes where a simple hose can't reach them. A quality diffuser with porous design ensures argon flows evenly in all directions, eliminating those stubborn air pockets that cause contamination.
This isn't just theory - it's the difference between getting your weld approved on the first inspection and having to explain why your stainless steel looks like it was welded in a rainstorm.
Here's where things get serious. For critical stainless steel welding, you need oxygen levels below 100 ppm. That's parts per million - we're talking about precision that matters when lives and livelihoods depend on your welds.
The old lighter test that some welders still rely on? It's completely useless for modern welding standards. A flame needs over 18.8% oxygen to stay lit - that's 180,000 ppm, nearly 2,000 times higher than what you actually need for quality work. A discussion on back purging stainless steel confirms that proper purging requires much lower oxygen levels than basic flame tests can detect.
For truly critical applications, you need an oxygen monitor that can measure down to 0.01% (100 ppm). These digital monitors give you the precision necessary to know your purge is actually working, not just hope it's good enough.
The proven method is running about 5 volumes of purge gas through your workpiece, nice and slow to minimize turbulence. This systematic approach ensures complete air displacement and creates the inert environment your welds deserve.
Let's talk about what really matters on the job site - your time and your wallet. A quality argon purge diffuser system pays for itself through reduced gas consumption, faster purge times, and elimination of costly rework.
When you use a diffuser instead of an open hose, you achieve effective purging faster and with less gas. The uniform distribution means you're not wasting argon trying to chase stubborn air pockets around the pipe. You get consistent results every time, which means consistent quality.
The real savings come from first-pass quality. When your purge is consistent and effective, you don't grind out contaminated welds and start over. You don't have awkward conversations with inspectors about why your stainless steel looks like it was attacked by rust. You don't order replacement fittings because the originals failed pressure testing.
In industries like aerospace, pharmaceutical, and food processing, where weld quality isn't negotiable, the cost of rework can be astronomical. A diffuser system that prevents a single rejected weld has already paid for itself many times over.
The bottom line? Professional welders use professional tools because they understand that minimizing wasted argon and eliminating rework isn't just about saving money - it's about building a reputation for quality work that keeps customers coming back.
When you're looking at a complete argon purge diffuser system, you're seeing the result of decades of field experience distilled into a few key components. Each piece has a specific job, and when they work together properly, you get the kind of consistent results that make the difference between amateur work and professional-grade welding.
The beauty of a well-designed purge system is its simplicity. You've got your diffuser head doing the heavy lifting of creating uniform gas flow, a quality hose that won't let you down, fittings that connect fast and stay connected, and control valves that put the power right in your hands. But here's the thing - not all components are created equal, and the quality of each piece determines whether your system performs when it counts.
The diffuser head is where the magic happens. This isn't just a piece of metal with holes drilled in it - quality diffusers use sintered stainless steel construction. Think of it like a high-tech sponge where metal particles are fused together under extreme heat and pressure to create thousands of tiny, controlled openings.
This sintered construction is what transforms a harsh blast of gas into gentle, uniform streams that won't create turbulence. When you're working with specialty alloys, this controlled flow is what prevents contamination and gives you that mirror-finish root pass.
Bar-style diffusers are particularly clever for pipe work. These slim designs can slip into pipes as small as 1.5" diameter while still providing the coverage you need for larger applications. The secret is having multiple gas distribution points along the length - it's like having several small diffusers working together instead of one big one trying to do everything.
Your gas hose needs to be more than just a conduit - it's got to handle the temperature swings and rough treatment that come with welding work. Quality systems use reinforced hoses that maintain consistent flow and won't collapse or kink when you need them most.
Quick-connect fittings are one of those innovations that make you wonder how we ever lived without them. When you're setting up a purge system on a job site, you don't want to be fumbling with threaded connections that leak or take forever to assemble. Push-to-connect fittings get you online fast and keep you focused on welding.
The integrated needle valve puts control right where you need it. Having a shut-off valve at the work area means you're not walking back to the gas bottle every time you need to adjust flow. In industrial settings where your gas manifold might be hundreds of feet away, this convenience becomes a real time-saver.
Feature | Sintered/Porous Plug | Multi-Port Bar | Jumbo Diffuser |
---|---|---|---|
Pipe Size Range | 1"-3" | 1.5"-6" | 3"-24" |
Flow Type | 360° radial | Linear multi-point | High-volume radial |
Best For | Small tube/pipe | Medium pipe runs | Large vessels |
Portability | Excellent | Good | Limited |
Single diffusers are the workhorses for smaller applications. When you're dealing with sanitary tubing, small process piping, or any application where you need to move your setup frequently, these compact units deliver professional results without the bulk. They're perfect for food processing, pharmaceutical work, and precision manufacturing where portability matters as much as performance.
Multi-port bar diffusers hit the sweet spot for medium-sized pipe work. These systems distribute gas through multiple controlled points along their length, creating overlapping zones of coverage that eliminate dead spots. If you're working on 2" to 6" pipe regularly, this configuration gives you the best balance of coverage and efficiency.
Jumbo diffusers are built for the big jobs - think 12" to 24" pipe where you need serious volume and uniform coverage across a large cross-sectional area. These aren't portable systems you'll be carrying around, but when you're working on large vessels or heavy industrial piping, they deliver the performance that's kept welders satisfied for over 25 years.
The key is matching your diffuser to your work. A system that's perfect for 2" sanitary tubing will struggle with 18" process piping, and a jumbo system is overkill for small tube work. That's why we engineer different configurations - because real welding work doesn't come in one-size-fits-all packages.
Choosing the right argon purge diffuser isn't a one-size-fits-all decision. After two decades in the field, I've learned that the wrong diffuser can turn a straightforward job into a nightmare of rework and frustration. You need to match your tool to your specific application, not just grab whatever's handy.
The applications we see at Tentacle Tools run the gamut - from delicate pharmaceutical tubing that requires surgical precision to massive industrial vessels where you're moving serious volumes of gas. Each job has its own personality and demands, and your diffuser system needs to match that personality perfectly.
Think about it this way: you wouldn't use a finishing hammer to drive railroad spikes, and you shouldn't use a small-bore diffuser on a 20-inch pipe. The physics just don't work, and you'll end up with inconsistent purging that shows up as contamination on your root pass.
Pipe size compatibility is your starting point, but it's not as simple as just measuring diameter. Our systems handle 1.5" to 24" pipes, but the real question is whether your diffuser can create proper flow patterns for your specific size range. A diffuser that's too small won't give you adequate coverage, while one that's oversized might not fit through your access points or create the laminar flow you need.
Material type drives everything else about your purge requirements. When you're welding stainless steel, you're playing in the big leagues - contamination shows up immediately and affects both appearance and performance. Titanium and Inconel are even less forgiving. These specialty alloys demand precision that would make a Swiss watchmaker proud.
Carbon steel applications might give you a little more wiggle room, but why settle for "good enough" when you can have perfect every time?
Job site conditions matter more than most welders realize. In industrial settings, your gas supply might be hundreds of feet away from where you're actually welding. Having on-site gas control with integrated needle valves means you're not constantly hiking back to the manifold every time you need to adjust flow or shut down for a break.
Portability becomes critical when you're working in tight spaces or moving between multiple joints. A system that's perfect for shop work might be completely impractical for field applications where you're crawling through pipe racks or working in confined spaces.
Durability isn't negotiable in industrial environments. Your diffuser system needs to survive being dropped, stepped on, and subjected to the general abuse that comes with real-world welding. That's why we build our systems with American-made quality - because tools that break down on the job site cost you money and credibility.
Flow rate control lets you fine-tune your purge for different applications. High-volume applications need different flow characteristics than precision work on small-diameter tubing. Having that control built into your system means you can adapt to different jobs without changing equipment.
TIG welding is where argon purge diffusers really shine. The precise heat input and clean arc characteristics mean that any contamination shows up immediately. You can't hide behind heavy filler passes or high travel speeds - the quality of your purge is on full display.
Orbital welding systems take this precision requirement to the next level. These automated systems can't compensate for variations in purge quality the way a skilled welder can. Your diffuser system must deliver absolutely consistent results every single time, because the machine isn't going to adjust for your inconsistent purging.
Sanitary tubing applications in food processing and pharmaceutical work often come with specific documentation requirements. You're not just creating a good weld - you're creating a weld that meets regulatory standards and can be verified through testing. This demands diffuser systems that can achieve and maintain specific oxygen levels throughout the entire welding process.
Aerospace applications represent the pinnacle of welding precision. Every aspect of the process, including purging, must be controlled, documented, and verified. These applications require diffuser systems that integrate seamlessly with quality control procedures and deliver results that can withstand the most rigorous inspection standards.
High-purity applications in semiconductor manufacturing, medical device production, and precision instrumentation push the boundaries of what's possible with purge welding. These jobs often require continuous oxygen monitoring and documentation, with tolerance levels that would have been impossible to achieve just a few years ago.
The bottom line is this: your argon purge diffuser needs to match not just your pipe size, but your entire welding process. When you choose the right system from Tentacle Tools, you're getting equipment that's been engineered by professionals who understand the demands of real-world welding and built to deliver the precision you need for critical applications.
When I look back at my 20 years in the oil and gas industry, I can tell you that the difference between a good welder and a great one often comes down to understanding that welding is a system - and purging is a critical part of that system. An argon purge diffuser isn't just another tool in your kit; it's your insurance policy against contamination, rework, and failed inspections.
The benefits we've covered aren't just theory - they're real advantages that impact your bottom line every day. Superior weld quality means passing inspection on the first try. Reduced gas consumption keeps more money in your pocket. Faster purge times mean you can move on to the next job quicker. And the confidence that comes from using professional-grade equipment? That's priceless.
Whether you're working on sanitary tubing in a food processing plant, critical piping in a pharmaceutical facility, or high-pressure systems in the oil and gas industry, having the right purging system is what separates the professionals from the weekend warriors. When you're dealing with stainless steel, titanium, or Inconel, there's no room for guesswork.
At Tentacle Tools, we understand these demands because we've been there. We've felt the frustration of contaminated welds and the pressure of tight deadlines. That's why our argon purge diffuser systems are engineered by welders, for welders, using American-made quality that stands up to the rigors of daily use.
The cost savings from eliminated rework alone make quality purging equipment a smart investment. But more importantly, the professional results you'll achieve will set you apart in an increasingly competitive industry. Your reputation as a welder depends on the quality of every weld you make - don't leave that to chance.
We're not just selling tools; we're providing solutions that help skilled tradespeople do their best work. When you choose equipment that's built by people who understand what it takes to get the job done right, you're investing in your craft and your future.
Find professional-grade purging equipment in our catalog and experience the difference that proper purging makes. Because in welding, as in life, the right tool for the job makes all the difference. When it comes to purging, that tool is a quality argon purge diffuser system designed and built by Americans who believe in hard work, quality craftsmanship, and getting the job done right the first time.
Explore insights, tips, and trends in tech and productivity!